Wastes from fields and wastes from processing are the two kinds of agricultural wastes. Field wastes are present after harvesting crops and include stems, leaves, and stalks, and waste after processing crops includes seeds, peels, husks, etc.
Recent innovations in turning Agricultural Waste into Biofuels
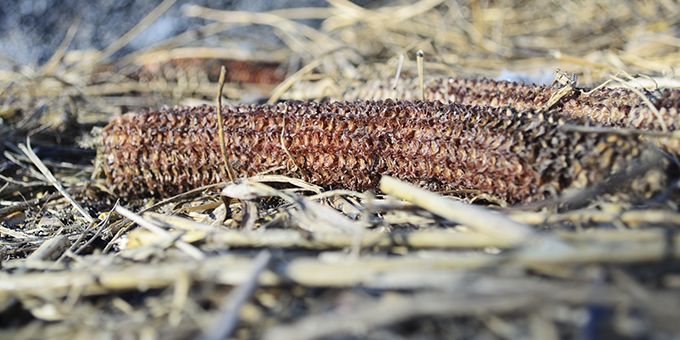
Dr. Raj Shah, Ms Amanda Loo | Koehler Instrument Company
Introduction
Globally, agriculture produces on average 23.7 million tons of food every day while also producing 21% of the world’s greenhouse gas emissions [1]. Lignocellulosic biomass is composed of four different categories that include agricultural wastes, hardwood, softwood, and grass [2]. These biomasses normally do not receive treatment and are disposed of, which can contaminate the environment and cause environmental load. Wastes from fields and wastes from processing are the two kinds of agricultural wastes. Field wastes are present after harvesting crops and include stems, leaves, and stalks, and waste after processing crops includes seeds, peels, husks, etc. [3]. The lignocellulosic biomass consisting of hemicellulose, cellulose, and lignin from agricultural waste can be converted into biofuels [4].
Pretreatment processes are typically required before converting agricultural waste into biofuels as these processes break down the waste into smaller components. Microwave pyrolysis is a very popular thermochemical method to convert biomass into biofuels, specifically biochar, bio-oil, and syngas. Many pathways have also been studied to convert biomass feedstock such as oil, syngas, alcohols, and sugars into aviation fuels.
Pretreatment Processes
From lignocellulose wastes, substances such as methane, carbohydrates, enzymes, amino acids, etc. can be obtained [5]. However, lignocellulose wastes are often disposed of, limiting their use potential. As previously mentioned, lignocellulosic biomass can be converted into biofuels as well demonstrating great advantages. Furthermore, lignocellulose materials are CO2 neutral as the CO2 from the biomass does not add any additional carbon to the carbon cycle [6].
Breaking down the cell wall of the biomass is complicated and requires pretreatment before converting it into biofuels. Physical, chemical, and biological approaches are common in the pretreatment process of lignocellulosic biomass. The major goals of pretreatment are to form sugars with hydrolysis, to use energy efficiently, and to reduce biofuel production costs [7]. Physical pretreatment is relatively inexpensive and convenient and includes radiation, milling, and grinding. Wheat straw has been previously studied, and it was determined that there was a 53% increase in biofuel yield with pretreatment at 180℃ than without pretreatment [8].
Figure 1. Illustrated structural difference between lignocellulose biomass before and after pretreatment methods [2].
More green pretreatment methods have been studied in recent years, which include ultrasound, electron beam, and pulsed-electric field technologies. A significant shortcoming of these green technology approaches is that they demonstrate poor efficiency and limited industrial scaling ability. As Figure 1 shows, pretreatment breaks down the biomass into its hemicellulose, cellulose, and lignin components, making it easier for conversion into biofuel.
An increasingly popular chemical pretreatment method is using dilute acid. Dilute sulfuric acid (H2SO4) is commonly used and the reason for using dilute acid instead of concentrated acid is because it provides a higher reaction rate with a shorter reaction time. Switchgrass, corn stover, and rapeseed straw have been studied with this pretreatment method and enzymatic hydrolysis of these lignocellulosic biomasses has been reported with high yields of pentose sugar [6]. Dilute acid pretreatment is commonly used to make bioethanol [7]. Another chemical pretreatment method is ammonia-based pretreatment that is non-corrosive and inexpensive. This method is efficient with biomass of agricultural wastes with low lignin content. The ammonia molecules dissociate into H+ and NH2 that gives rise to chemical bond breakage in sugar and lignin [6].
Ammonia fiber explosion/expansion (AFEX) is a physico-chemical pretreatment that branched off the ammonia-based chemical pretreatment [7], with the main difference being that AFEX instead uses anhydrous liquid ammonia. Switchgrass and corn stover have been commonly used for this method. It works by exposing the anhydrous liquid ammonia to the biomass at 60-120℃ and high pressure which gives good ethanol yields from the input biomass. AFEX is efficient for lignin removal, but one disadvantage that this pretreatment method has is that it brings about environmental concerns because of its use of ammonia [2].
Microwave Pyrolysis
The process of biochemical conversion requires pretreatment processes for the lignocellulosic components and is not as efficient compared to thermochemical conversion. Biomass recalcitrance, where the cell wall of crops and plants resists enzymatic degradation to process the biomass, limits the efficiency of biochemical conversion [9]. Instead, thermochemical conversion methods are used to convert agricultural waste to biofuels, and the main five processes are combustion, pyrolysis, gasification, combustion, and hydrothermal liquefaction [4].
Pyrolysis technology can be used to treat plastic, waste biomass, and agricultural wastes that create a barrier preventing heat from escaping from the outer surface of the material to the core. Microwave pyrolysis, a specific pyrolysis reactor design, is simpler and more efficient than conventional pyrolysis and works by creating heat inside the material [10]. Furthermore, microwave pyrolysis has high energy efficiency and produces less NOx and SOx emissions than combustion produces [4].
Microwave pyrolysis converts agricultural waste of hemicellulose, cellulose, and lignin into biochar, bio-oil, and syngas, all of which are beneficial pyrolysis products. The microwave process of heating occurring within the material is more efficient and quicker than conventional pyrolysis [11]. Biochar is a solid that is typically used for cooking fuel or soil conditions, and bio-oil is a liquid used as a combustion fuel substitute in boilers and furnaces [9]. Hemicellulose typically converts to non-condensable syngas and bio-oil, cellulose to syngas and bio-oil as well as biochar, and lignin primarily converts to biochar. Table 1 shows some typical agricultural wastes and their lignocellulosic component percentages, along with their pyrolysis product yield percentages.
Table 1. Pyrolysis product yield percentages of different agricultural wastes according to the pyrolysis type and lignocellulose component percentages [4].
Pyrolysis heats biomass using external heating sources like electrical energy and has high energy consumption. To counter this, solar photovoltaic (PV) electricity can be used as an electrical energy source for microwave-assisted pyrolysis (MAP). Solar PV is beneficial for rural areas as this reduces their reliance on conventional power inputs [9]. Rice straw is a common crop residue and was used to study the effectiveness of solar PV as an electricity source for MAP. An increase in bio-oil yield occurred at a microwave power of 300-700 W, while a decrease in biochar yield happened at the same power range with or without additives in both cases. A 71.52% energy recovery concerning the energy of raw rice straw when using solar PV was also found, compared to only a 56.32% energy recovery with grid electricity.
Another study using solar-powered microwave pyrolysis was done, but corn stover was studied instead of rice straw. The goal was to maximize wood vinegar and biochar products from corn stover as biomass feedstock that is plentiful in India. Normally corn stover is burned to dispose of, but this is harmful to the environment and can be made into more valuable products such as wood vinegar. Wood vinegar is produced from bio-oil with a sedimentation process: after crude bio-oil sits for 2-3 months, two layers form where the red-brown upper layer is wood vinegar, and the brown bottom layer is tar. This wood vinegar is valuable in the agricultural sector as it can be used as a wood preserver, herbicide, or food flavoring agent. The biochar can potentially be used as a source for solid biofuel.
The experiment consisted of using 5% biochar used as an additive for higher bio-oil yield because it is relatively cheap and easily accessible. The biochar additive was used for microwave absorption during pyrolysis. Different reaction times of 15, 20, and 25 minutes and different microwave power values of 300, 500, 700, and 900 Watts were observed. The additive ratio was also tested, with values of 5, 10, 15, 20, and 25%. It was determined that the ratio of 5% additive resulted in a 31 wt% of wood vinegar yield and only a 28 wt% yield without additive. This additive ratio was then used as a standard for the experiment with the results shown below in Figure 2.
Figure 2. Biochar, bio-oil, and gas yields under different microwave pyrolysis conditions without additive and with additive [12].
A general trend of an increase in bio-oil production is seen with the presence of the bio-char additive. Additionally, yields of 31 wt% of wood vinegar and 34 wt% of biochar were found. The results of the experiment demonstrate that the use of a renewable and plentiful source can effectively produce valuable pyrolysis products for the agricultural sector and to create biofuel.
Aviation Fuels
Commercial airline aviation fuel consumption was 260 million m3/year in 2005, which has increased to more than 340 million m3/year in 2018 and is expected to continue to grow [13]. 669 million tons of CO2 are released by the aviation sector annually, with an expected six times increase by 2050 [14]. Road, rail, and maritime sectors all use biofuels, but the most promising changes are expected to be seen in the commercial aviation sector in reducing greenhouse gas emissions and reducing oil dependency [15]. However, the ASTM (American Society for Testing Materials) and EU standards of bio-aviation fuels are that they need to be hydrocarbons without oxygen, making it difficult to produce from biomass as biomass has a high wt% of oxygen [13]. The ASTM D1655-09 lists the specifications of jet fuels, such as density, viscosity, energy density, etc. that must be met by the aviation industry [14].
Figure 3. Jet fuel Jet A-1 hydrocarbon composition [14].
Figure 3 shows the composition of a common Jet A-1, a standard jet fuel that consists of hydrocarbons in the C9-C16 range. Lignin is typically converted to cycloalkanes and aromatics while cellulose and hemicellulose are converted to n-alkanes and iso-alkanes. Typically, the volume percent compositions of the different hydrocarbons are 20 vol% n-alkanes, 40 vol% iso-alkanes, 20 vol% cycloalkanes, and 20% aromatics.
Petroleum is composed of deoxygenated hydrocarbons while biomass has oxygenated hydrocarbons, meaning that different conversion technologies are required to convert biomass into fuels compared to using petroleum in fuels (Figure 4). The common feedstocks for each route are waste, algal, and plant oils for oil-to-aviation pathway, CO and H2 for syngas-to-aviation pathway, C2-C5 alcohols for alcohols-to-aviation pathway, and finally both bioconversion and catalytic conversion use sugars but the catalytic approach can also use sugar derivatives for the sugars-to-aviation fuel pathway [16]. At a broader look, feedstocks for bio-aviation fuel are oil-based, solid-based, and gas-based feedstocks. Oil-based feedstocks include vegetable and algal oils, solid-based include lignocellulosic biomass, and gas-based include syngas and biogas [17].
Figure 4. Biomass to aviation fuels conversion routes [16].
In oil-to-aviation fuel conversion, catalytic hydrotreating is performed at temperatures of 250-400℃ with high pressure, resulting in a product referred to as hydroprocessed renewable jet fuel. Noble metal-supported and alumina-supported metals are used as catalysts. The unsaturations in the vegetable oil feedstocks transform into branched hydrocarbons during the hydrotreating process. One shortcoming of the oil-to-aviation process is that hydrotreating does not produce cycloalkanes or aromatics. The process of gas-to-jet includes the gasification of biomass to syngas, then undergoing Fischer-Tropsch synthesis of syngas to hydrocarbons of the C1-C50 range. Gasification converts a carbon source into a gas at high temperatures. However, impurities present in biomass and the oxygenated hydrocarbons limit the efficiency of the Fischer-Tropsch process. The high heat of the Fischer-Tropsch process must be removed because methane may form, and catalysts may deteriorate. The gas-to-jet is a challenging route for jet fuel production because of additional steps that must be taken to mitigate these problems. Furthermore, this process does not produce aromatics.
The alcohol-to-jet process can convert oxygenated fuel to hydrocarbons that are compatible with today’s transportation fuels. Finally, the sugar conversion pathway of sugars to hydrocarbons is complex as there are only six carbon atoms in sugars and their derivatives, while jet fuels require longer carbon chains. Removing oxygen from the products with processes such as hydrogenation and dehydration must then be done [14].
In a 2020 experiment using waste cooking oil from Egyptian fast-food restaurants to create jet fuel, 2.5% w/v zinc aluminate (ZnAl2O4) nanoparticles were used as catalysts because they can decrease the H/C ratio in thermal cracking [17]. The waste cooking oil consisted of 39.8% C8-C16, 60.1% C17-C19, and had a 10.6 wt% oxygen. It was found that thermal cracking at temperatures of 400-450℃ was most effective at cracking long carbon chains to shorter chains of C8-C16. After the initial thermal cracking process, 96% crude biofuel was obtained, and after distillation, 49% bio-aviation fuel and 51% biofuels for other purposes was obtained. The experiment concluded that bio-jet fuel from hydrocracking of the waste cooking oils had small oxygen content and lacked corrosive materials, demonstrating high-quality oil products.
Conclusion
The pretreatment processes needed for biochemical conversion methods break down the lignocellulose biomass feedstock into smaller components, making it easier to convert the input biomass into biofuels. Dilute acid, acid, ammonia-based, and ammonia fiber explosion/expansion pretreatment methods have been discussed, each with its advantages and disadvantages. Due to the inefficiency that arises from biomass recalcitrance, thermochemical conversion methods such as microwave pyrolysis can be used. Experiments using solar power as an energy source with rice straw and corn stover have been performed where large wt% values of biofuel products were produced. Furthermore, the four major routes for aviation fuel conversion are reported because of the high potential to reduce greenhouse gas emissions at a massive scale.
About Dr. Raj Shah
Dr. Raj Shah is a Director at Koehler Instrument Company in New York, where he has worked for the last 25 years. He is an elected Fellow by his peers at IChemE, CMI, STLE, AIC, NLGI, INSTMC, The Energy Institute and The Royal Society of Chemistry An ASTM Eagle award recipient, Dr. Shah recently coedited the bestseller, “Fuels and Lubricants handbook”, details of which are available here.
A Ph.D in Chemical Engineering from The Penn State University and a Fellow from The Chartered Management Institute, London, Dr. Shah is also a Chartered Scientist with the Science Council, a Chartered Petroleum Engineer with the Energy Institute and a Chartered Engineer with the Engineering council, UK. An adjunct professor at the Dept. of Material Science and Chemical Engineering at State University of New York, Stony Brook, Raj has over 400 publications and has been active in the petroleum field for 3 decades. More information on Raj can be found at here.
About Amanda Loo
Ms. Amanda Loo is a student of Chemical engineering at SUNY, Stony Brook University, where Dr. Shah is the current chair of the External Advisory board of directors for the department. She is currently an intern at Koehler Instrument Company.
References
[1] Duque-Acevedo, M., Belmonte-Urena, L. J., Cortés-García, F. J., & Camacho-Ferre, F. (2020). Agricultural waste: Review of the evolution, approaches and perspectives on alternative uses. Global Ecology and Conservation, 22, e00902.
[2] Hassan, S. S., Williams, G. A., & Jaiswal, A. K. (2018). Emerging technologies for the pretreatment of lignocellulosic biomass. Bioresource Technology, 262, 310-318.
[3] Rao, P., & Rathod, V. (2019). Valorization of food and agricultural waste: a step towards greener future. The Chemical Record, 19(9), 1858-1871.
[4] Ge, S., et al. (2021). Progress in microwave pyrolysis conversion of agricultural waste to value-added biofuels: A batch to continuous approach. Renewable and Sustainable Energy Reviews, 135, 110148.
[5] Aftab, M. N., Iqbal, I., Riaz, F., Karadag, A., & Tabatabaei, M. (2019). Different pretreatment methods of lignocellulosic biomass for use in biofuel production. Biomass for Bioenergy-Recent Trends and Future Challenges.
[6] Sasmal, S., & Mohanty, K. (2018). Pretreatment of lignocellulosic biomass toward biofuel production. In Biorefining of Biomass to Biofuels (pp. 203-221). Springer, Cham.
[7] Kumari, D., & Singh, R. (2018). Pretreatment of lignocellulosic wastes for biofuel production: a critical review. Renewable and Sustainable Energy Reviews, 90, 877-891.
[8] Mahmood, H., Moniruzzaman, M., Iqbal, T., & Khan, M. J. (2019). Recent advances in the pretreatment of lignocellulosic biomass for biofuels and value-added products. Current Opinion in Green and Sustainable Chemistry, 20, 18-24.
[9] Fodah, A. E. M., Ghosal, M. K., & Behera, D. (2021). Studies on microwave-assisted pyrolysis of rice straw using solar photovoltaic power. BioEnergy Research, 14(1), 190-208.
[10] Wang, Y., et al. (2018). Production of bio-oil from agricultural waste by using a continuous fast microwave pyrolysis system. Bioresource technology, 269, 162-168.
[11] Wu, C., Budarin, V. L., Gronnow, M. J., De Bruyn, M., Onwudili, J. A., Clark, J. H., & Williams, P. T. (2014). Conventional and microwave-assisted pyrolysis of biomass under different heating rates. Journal of Analytical and Applied Pyrolysis, 107, 276-283.
[12] Fodah, A. E. M., Ghosal, M. K., & Behera, D. (2021). Solar‐powered microwave pyrolysis of corn stover for value‐added products and process techno‐economic assessment. International Journal of Energy Research, 45(4), 5679-5694.
[13] Wang, M., Dewil, R., Maniatis, K., Wheeldon, J., Tan, T., Baeyens, J., & Fang, Y. (2019). Biomass-derived aviation fuels: Challenges and perspective. Progress in Energy and Combustion Science, 74, 31-49.
[14] Díaz-Pérez, M. A., & Serrano-Ruiz, J. C. (2020). Catalytic production of jet fuels from biomass. Molecules, 25(4), 802.
[15] Kousoulidou, M., & Lonza, L. (2016). Biofuels in aviation: Fuel demand and CO2 emissions evolution in Europe toward 2030. Transportation Research Part D: Transport and Environment, 46, 166-181.
[16] Wang, H., Yang, B., Zhang, Q., & Zhu, W. (2020). Catalytic routes for the conversion of lignocellulosic biomass to aviation fuel range hydrocarbons. Renewable and Sustainable Energy Reviews, 120, 109612.
[17] El-Araby, R., Abdelkader, E., El Diwani, G., & Hawash, S. I. (2020). Bio-aviation fuel via catalytic hydrocracking of waste cooking oils. Bulletin of the National Research Centre, 44(1), 1-9.
The content & opinions in this article are the author’s and do not necessarily represent the views of AgriTechTomorrow
Comments (0)
This post does not have any comments. Be the first to leave a comment below.
Featured Product
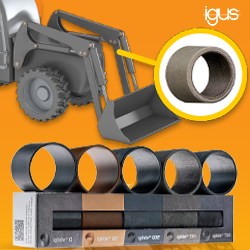