Infarm wants to put a farm in every grocery store
Steve O'Hear for TechCrunch: Imagine a future where you go into a grocery store to buy some fresh basil, and, as you traverse the aisle, instead of polythene bags containing mass-produced snippets of the herb that have been flown in from thousands of miles away, in front of you are a stack of illuminated containers, each housing a mini basil farm.
The plants themselves are being monitored by multiple sensors and fed by an internet-controlled irrigation and nutrition system. Growing out from the centre, the basil is at ascending stages of its life, with the most outer positioned leaves ready for you, the customer, to harvest.
Now imagine no more, because, to paraphrase science fiction writer William Gibson, the farm of the future is already here, it’s just not evenly distributed.
Infarm, a 40-plus person startup based in Berlin is developing an “indoor vertical farming” system capable of growing anything from herbs, lettuce and other vegetables, and even fruit. The concept might not be entirely new — Japan has been an early pioneer in vertical farming, where the lack of space for farming and very high demand from a large population has encouraged innovation — but what potentially sets Infarm apart, including from other startups, is the modular approach and go-to-market strategy it is taking.
This means that the company can do vertical farming on a small but infinitely expandable scale, and is seeing Infarm place farms not in offsite warehouses but in customer-facing city locations, such as grocery stores, restaurants, shopping malls, and schools, enabling the end-customer to actually pick the produce themselves.
“When we presented our idea three or four years ago, people looked at us as though we [had] lost our mind,” says Infarm co-founder Erez Galonska. “We are the first company in the world that has put vertical farming in a supermarket. We did it last year with Metro Group, which is one of the biggest wholesalers in Europe, and now we are facing very big demand from other supermarkets that want to do the same”. Full Article:
Comments (0)
This post does not have any comments. Be the first to leave a comment below.
Featured Product
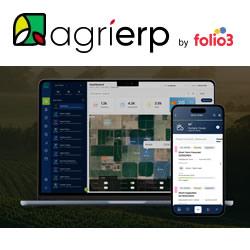