WCCO Belting Announces Patent-Pending Draper Belting and Belted Chain Technology for Agriculture Industry
Innovation on display at Agritechnica in Hanover, Germany, November 10-16
WAHPETON, ND - November 11, 2019 - WCCO Belting announced two new products - a angled cleat extension for its RAPTOR® draper belting and a new belt design for belted chain assemblies for the agriculture industry - at the world's leading trade fair for agricultural technology, Agritechnica. These designs, both patent-pending, demonstrate WCCO Belting's commitment to be the leading value innovator for agricultural belting solutions worldwide
WCCO Belting's patent-pending enhancement for draper belting is an angled cleat technology manufactured with the company's RAPTOR® belt construction, the gold standard in harvesting applications for small grains and edible beans. For combine harvest headers (draper platforms), swathers, and mergers, the cleat extension is designed to increase efficiency and output while reducing downtime from material buildup under the belt. The angled cleat directs crop to the center of the draper belt and into the feeder house, successfully pulling material away from the cutter bar. In addition, an angled connection method creates a smooth, quiet transition of the draper belt on the roller.
The design of its patent-pending belt for belted chain assemblies will improve process efficiency for assembly manufacturers and redefine performance for original equipment manufacturers and growers in root vegetable harvesting applications including potatoes, sugar beets, carrots, onions, and more.
The belt can universally accommodate any pitch requirement and is engineered with a simple hardware concept for easy assembly and disassembly. The construction of WCCO Belting's belt for belted chain is a strong, yet flexible design that supports the belt's ability to move around the rollers for less pressure on the splice. Low elongation in the fabric design reduces slippage and promotes steady tension during operation. In addition, sealed edges prevent moisture wicking into the belt carcass, which eliminates delamination.
"We are excited to announce these products at Agritechnica, a fair that celebrates the future of agricultural technology," said Jean Voorhees, Vice President of Business Development at WCCO Belting. "As a company dedicated to value innovation, we are proud to see our latest solutions help move agricultural equipment - and the entire industry - forward."
The products are available for equipment manufacturers and belted chain component manufacturers. For more information, stop at WCCO Belting's booth at Agritechnica in Hall 05 at Stand C13, visit www.wccobelt.com and follow the company on LinkedIn.
About WCCO Belting
WCCO Belting is a 65-year-old, family-owned and award-winning custom rubber product manufacturer for the agriculture, light industrial, construction, sand and gravel, packaging and recycling industries worldwide. The company is the value innovator in the global rubber belting industry, engineering custom products using specialized equipment and proprietary processes. WCCO focuses on the technological advancement of each raw material and belt component to provide high value rubber product solutions. Its design and manufacturing expertise are effective in lowering the total cost of ownership of their customers' equipment.
Featured Product
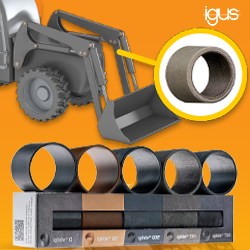
igus® - Free heavy-duty plastic bearings sample box
The iglide® heavy-duty sample box provides a selection of five unique iglide bearings, each suitable for use in heavy-duty equipment due to their self-lubricating, dirt-resistant properties. Each bearing material boasts unique benefits and is best suited for different application conditions, though each can withstand surface pressures of at least 11,603 psi at 68°F.