Staying competitive means maximizing your available grow room space. Cannabis cultivators and indoor food producers who can increase yields without sacrificing product quality or adding square footage are on the path to increased ROI.
4 Ways to Maximize Grow Room Square Footage
Article from | Surna
Maximizing the square footage of your commercial grow rooms can help improve your ROI. This means that you are squeezing as many plants into the grow space as possible without sacrificing quality or yield.
There are several reasons why you may want to maximize your canopy footprint. For example, in regions where real estate comes at a premium, such as in cities like Los Angeles or New York, every square foot can make a difference on your bottom line. Or you may be hoping for bigger yields without having to expand your operation.
Regardless of your reason, there are 4 key methods to ensuring you get the most out of your indoor farm.
1. Go Vertical
Indoor farms have the luxury of being able to grow in tiers. Multi-tier vertical grow racks allow you to expand your plant canopy without adding square footage. Instead, you are expanding your canopy in cubic feet.
If you are growing leafy greens, microgreens, herbs, soft fruits, etc., you will most likely opt for a vertical farm. Because these plants are typically short and compact, they are very easy to grow in layers that don’t require much spacing between them. Therefore, you can fit a lot of them in one room.
However, if you are cultivating cannabis, you have a bit harder of a choice to make. Cannabis plants are tall and require more vertical height than many other plant varieties that can be grown in controlled environments. This means that you will be able to fit less tiers of plants in a room. Commercial cannabis growers must take into consideration what kind of racks they will use, their water volumes, and their HVAC requirements before deciding what will be best for their ROI.
Grow Room Equipment for Vertical Farming
If you are deciding whether to grow vertically, consider the grow room equipment you will need:
- Vertical Grow Racks: You will need to invest in multi-tier grow racks. There are many options ranging in brand, quality, mobility, height, and irrigation method. Additionally, you will need to ensure your staff can access each tier via ladders, lifts, or some other method of vertical transportation.
- LED Lights: Traditionally, high-powered HPS lights were the preferred lighting method in horticultural operations. However, LEDs have become more popular thanks to their energy saving potential and reduced waste heat. Because they emit less heat than other light sources, LEDs decrease vertical space requirements between the light and the plants. This allows you to grow in vertical layers rather than being limited to single-tier indoor grows and greenhouses.
- HVAC: Adding more plants, more lights, and more water to a room will impact your HVAC requirements. Your system will need to handle a higher cooling load and to account for more humidity. You will also need adequate air movement to avoid pockets of hot, humid air from forming, which usually requires a special system that incorporates both the grow rack and ventilation.
2. Create Moveable Aisles
Most commercial indoor farms use mobile benches and vertical grow racks these days. Pushing rolling benches and mobile racks from side to side allows you to create aisles where needed, expanding your cultivation space without the need for additional floor space. There are a few ways grow benches can be mobilized.
Rolling benches are the most common method among single-tier options. The feet are attached to the floor, while a rolling bar beneath the table allows the tray top to move from side to side, creating a domino effect along the other tables in the room.
Track benches work similarly, however instead of having stationary legs, the table top is stationary, and the legs can be moved along a track within the floor. Mobile vertical grow systems move in the same way, except they are operated by a wheel and pully system rather than pushing the racks themselves. This makes it easy to move them, even when filled with plants.
Because mobile racks and benches allow you to maintain one aisle per room, you can fit many more rows of plants inside of the grow space. It is important that you work with your mechanical engineer to ensure that you are providing proper cooling, dehumidification, and air circulation evenly throughout the room.
3. Optimize Your Layout
When designing the layout of your facility, keep your workflow in mind. Your architect should understand plants’ growth cycles when they are creating your floor plan.
For example, a vertically integrated cannabis producer may require dedicated rooms for clones, veg, flower, drying, and extraction, all securely separated from a dispensary retail front. These rooms usually have different size requirements. For instance, because its typical to dedicate one square foot of vegetative canopy for every four square feet of flowering canopy, veg rooms will be smaller and less numerous than flower rooms.
A facility layout that is optimized for labor can improve productivity and minimize costs so that you can get the most out of your farm. Also, room layouts should be designed with benching and lighting selections in mind. This will help you avoid wasted space or surprise hurdles that could undermine your bottom line.
4. Maximize Yields
Adding more plants to a room may not be the shortest route to success. In fact, adding more plants to a room, especially vertically, will put more strain on your HVAC system as they transpire more moisture into the air and require more lights. However, there are several methods that may increase your yields per plant.
Below are a few examples of areas that can play a major role in yield production. It is important to note that there are many variables that will affect your results including crop variety, environment, watering, nutrients, lighting, air flow, biosecurity, and more.
If you are an existing operator, R&D is key to determining which methods will be most successful for your operation, so be sure to test your methods on small sample crop before implementing changes throughout the rest of the grow.
If you are still planning your project, work closely with your facility design team to ensure they understand your expectations and planned grow methodologies.
Proper Climate Control
Healthy plants yield more than unhealthy plants. That may sound obvious, but this is the core reason why proper climate control is so important to the success of your indoor farm.
Environments that are too humid can inhibit a plant’s ability to transpire excess water back into the air, essentially causing it to drown and turn moldy. Environments that are too dry can cause transpiration rates to accelerate, drying the plant out. And temperature has a unique relationship to humidity and its impact on transpiration rates called vapor pressure deficit (VPD). Be sure to work with an engineering firm that has experience with indoor agriculture to avoid issues stemming from your mechanical system.
Not only this, but without the right air circulation system, pockets of air that varies in temperature and humidity called “microclimates” can form throughout the grow space. This is particularly problematic in poorly ventilated vertical farms in which warm air rises, causing a stratification of temperature and humidity. This can be controlled with well-placed fans, special racking ventilation, and a properly designed HVAC system.
Lighting
Some growers have claimed to maximize their yields through light manipulation. There are many aspects of lighting that can have an affect on your crop yields including:
- Grow light selection (brand, HPS vs. LED, PPD, etc.)
- Lighting layout
- Distance between plants and light fixtures
- Color spectrum
- Lighting and dimming schedules
There are many factors that will contribute to your plant’s health, but lighting recipes can make for an interesting area for experimentation.
Grow Methodology
There are many other aspects of your grow room and techniques that can have an impact on your crop yield. There are various methods of irrigation such as aeroponics and hydroponics. There are plant training methods that can affect the direction of growth and bud development. There are also many nutrient and fertilizer recipes.
At the end of the day, your head grower will be the best person to determine your grow methodology. They will have the most horticultural knowledge, and their preferences will act as a guiding force when your design team engineers your facility.
As previously mentioned, controlled R&D throughout the life cycle of your business will help you continue to improve and try new things. Just keep in mind that changes in water volumes, lighting, plant production, etc. can affect your HVAC loads to varying degrees. If you plan on making big changes, ideally, you should consult with your design team before your initial build out to ensure your system will be capable of offering that kind of flexibility.
Enjoy Maximum Results!
Most growers try to maximize their yields, but some run into hurdles such as under-budgeting, poor planning, or under-engineering. You don’t have to invest in the most expensive equipment to get the most out of your grow rooms, but you should choose your head grower and design teams carefully.
Communicating everyone’s expectations up front will make sure you know what set up makes the most sense for your business. Proper planning can help you maximize your square footage, and continual R&D can help you find areas for improvement. Ultimately, we hope you can confidently maximize your yields!
If you are building a new indoor farm, expanding, or need to retrofit an under-performing facility, contact us below. Our experienced team of engineers, architects, and project managers are ready to help bring your vision to life.
The content & opinions in this article are the author’s and do not necessarily represent the views of AgriTechTomorrow
Comments (0)
This post does not have any comments. Be the first to leave a comment below.
Featured Product
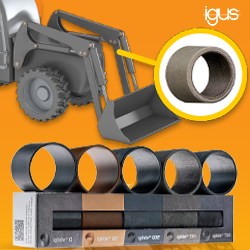