The vertical farming industry still has challenges to overcome. Production costs remain relatively high and, as a young market, knowledge gaps in operational best practices in critical areas threaten long-term sustainability and profitability.
Three Ways to Maximize a Vertical Farm’s Potential
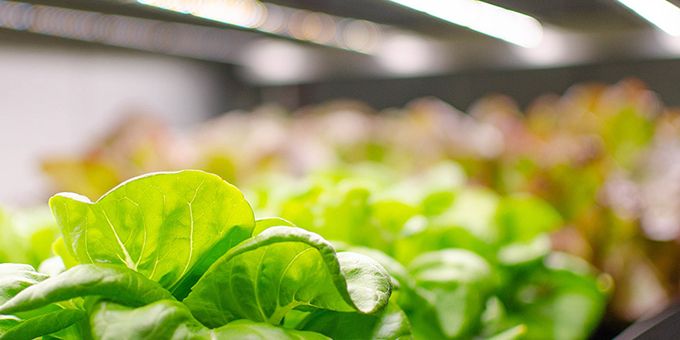
Abhay Thosar, Ph.D, Director of Horticulture Services | Fluence by OSRAM
Population growth and urbanization are forcing global food production to a crossroads. Overall, migration to high-density areas increases access to health care, higher-paying jobs, education and other socioeconomic opportunities. But it also places more strain on existing infrastructure and demand for resources, leading to greater water scarcity, energy consumption, waste and, perhaps most importantly, threats to food supply, prices and quality.
The economically disadvantaged will be the first to pay the price of increased urbanization. As prices increase and access to quality food sources decreases, the nutritional health of poor populations will decline. Over the next several years, the responsibility of bridging the gap between projected food supply and demand in urban areas will largely fall on vertical farms, an industry that is expected to nearly quadruple by 2025 to about $16 billion. The COVID-19 pandemic could accelerate that growth rate even further.
The vertical farming industry still has challenges to overcome. Production costs remain relatively high and, as a young market, knowledge gaps in operational best practices in critical areas like facility design and environmental conditions threaten long-term sustainability and profitability. The evolving economic dynamic with supermarkets is forcing vertical farms to scale quickly as they attempt to grow and supply a wider variety of crops while maintaining the buyer’s standards around produce size, quality and nutritional value. And, as we look to the future, new innovations in lighting strategies, facility design, cultivation best practices and automation mean that vertical farming operations have to be constantly adapting and seeking new operational advantages. This is just as true for new market entrants and relatively established players alike, and each will be critical to not only maintaining profitability, but ensuring that food production in urban areas can increase with demand.
With that in mind, here are three critical factors vertical farmers need to consider to meet market expectations, improve efficiency and ultimately grow, cultivate and distribute larger quantities of quality food to more people in a smaller area.

Facility design as a function of market demand
The history and growth of the vertical farming market are largely driven by two trends at the consumer and buyer levels. A decade ago, consumers asking questions about how, where and when their food was grown was practically unheard of. Things are different today. People want to know the provenance behind the food they buy and ensure it is chemical-free and safe to eat. Every product has become more than a label, it’s become a story that consumers want to hear, and one that has an equally significant impact in where they shop and what they buy.
Supermarkets have taken notice. Beyond that, though, vertical farming operations have given supermarkets one more option in addition to the existing supply chains on which they’ve relied for food production and distribution. Vertical farms play an even more important role during large-scale disruption events like the COVID-19 pandemic or massive recalls. As a result, supermarkets—which value the consistent supply of produce above all—are turning to their local vertical farming operations and, in some cases, even investing in them directly. The increased attention, however, comes at a cost (literally and metaphorically). Supermarkets are demanding that the vertical farms supplying them grow a wider variety of crops—lettuce, tomatoes, cucumbers, leafy greens, microgreens, herbs—more consistently while also meeting unique specifications around weight, aesthetic, nutritional value and a variety of other factors that are ultimately dictated by the vertical farm’s environment and the grower’s expertise.
Vertical farmers are quickly realizing they need to expand their portfolio from potentially a handful of crops to a few dozen or more, raising a range of questions on how to design or retrofit their facilities and adjust environmental conditions that favor any given crop.
The first decision many vertical farmers face is the growing technique that will be most scalable and viable for their operation. Hydroponics, aeroponics and aquaponics have all emerged as viable options with varying degrees of success, but they’re far from interchangeable.
In the end, there is no universal solution for every vertical farm. Cultivators should closely consider their buyers’ expectations, and how those expectations might change over time. Then, cultivators must assess the full range of their crops’ needs and how each might respond differently to various environmental factors and lighting strategies.

Strike a balance between environmental factors
The next set of factors governing facility design, investment and day-to-day operations should always be the environmental conditions themselves.
How air flows into and across each rack of a vertical farm is one of the most unique and important challenges vertical farms have to solve. Ignoring or failing to closely monitor air flow is often a death blow to entire sections of crops and to profitability, yield and consistency as a result. Air movement helps to maintain temperature, humidity and transpiration at each rack, and lack of it creates wide temperature swings or large gaps between crops at the bottom and crops at the top. It’s an incredibly fragile balance to strike. Everything from the number of access points into a warehouse—there should only be one access point—to HVAC and circulation systems affect air movement. As a best practice, the maximum difference between the temperature at the top-most rack and the bottom-most rack should be no more than two degrees Fahrenheit. In practical scenarios, cultivators facing large temperature fluctuations can also consider placing crops that prefer relatively warmer temperatures—such as basil, oregano, chives, sage or thyme—at the top and simply let the laws of thermodynamics do the rest.
Carbon dioxide enrichment is a slightly easier condition to manage but no less important and changes based on temperature and lighting strategy. CO2 enrichment, too, can fluctuate based on the number of access points into a warehouse (again, there should only be one). Enriching a cultivation environment with carbon dioxide stimulates photosynthesis and plant growth, the rate of which is critically dependent on the difference between CO2 concentrations in the air and in the leaf cells.
The law of diminishing returns puts a cap on the amount of carbon dioxide cultivators should be introducing. CO2 is by no means the only factor governing plant growth, but vertical farms have the advantage of being able to closely monitor and control CO2 levels. To do so properly, however, they shouldn’t shy away from significant investments in both handheld devices—which allow cultivators to measure carbon dioxide levels at each rack, each plant and each leaf—but also large-scale control systems that can measure and track CO2 throughout the entire warehouse.
Humidity levels govern a plant’s transpiration rate and the aperture sizes of its stomata, ultimately affecting how much water it moves from its root zone to release back into the warehouse. When a plant’s stomata open, they release water while also collecting carbon dioxide, making the balance of humidity, temperature and carbon dioxide all the more crucial. Different plant types in different growth stages have different transpiration rates, adding even more complexity to how a vertical farm is designed and managed. The most common way to express humidity is relative humidity, the percentage of water vapor in the air at a given temperature compared to the total amount of water the air can hold at that temperature. In vertical farming, however, vapor pressure deficit (VPD) is the more accurate way to gauge humidity’s effect on plant growth. VPD remains an interesting discussion among researchers as the industry seeks to understand the differences between VPDs for air and leaves as well as exact VPD calculations.
Every environmental factor in a vertical farm affects the others to some degree. Nearly everything can be controlled; it’s both the advantage and the challenge native to the market. No factor, however, is more important to photosynthesis than its primary driver: light. Each factor—CO2, temperature, airflow, humidity, fertilizer, irrigation, VPD—need to be fine-tuned with changes to light quantity and quality to optimize plant performance and response.
Designing an effective lighting strategy
The design and implementation of an effective lighting strategy is and always will be the primary driver of your vertical farm’s success. In environments as complex as vertical farms, identifying the correct light intensity, spectra, photoperiod and configuration will determine how other environmental factors work together to optimize a facility for plant yield and quality.
The first of these, the fixtures themselves, carry more implications for vertical farms than other cultivation spaces; in a vertical farm, plants receive no other source of light. The sun isn’t the safety blanket that it is for greenhouses. This simple and obvious fact means that vertical farmers have to find efficiencies in ways others don’t, which can manifest across a variety of operational metrics. Light efficacy, for instance, becomes more important. Most vertical farms are located in urban areas and are likely paying a premium for electricity. Maximizing micromoles per watt and reducing energy waste becomes more than a sustainability initiative, it’s critical to overall profitability.
Similarly, vertical farms operating warehouses measuring in the tens of thousands of square feet need fixtures with a good form factor without sacrificing light intensity. The right configuration means vertical farms can squeeze more racks into their facilities while also putting the lights closer to the plants for better results.

Beyond the hardware specifications, lighting design and strategy consist of several key factors: light intensity, light quality (or spectra) and light bar configuration. Each should be rooted in a facility’s overarching goals—typically defined by the consumer or buyer. Lighting strategies can be customized by crop, yielding specific plant chemistries or changes in biomass. Differences in spectra and light intensity can affect a crop’s coloration, shelf life, taste and smell. Desired crop characteristics should be determined up front in conjunction with the prospective buyer, therefore guiding a lighting designer to identify the optimal strategy to accomplish a facility’s goals.
Light quantity is the first and foremost aspect when it comes to optimizing the productivity of the crop. It is important to target the correct mols/day for each crop. Light quality (or spectra) is defined by measuring light’s wavelength in nanometers (nm). Wavelengths of light that drive photosynthesis are primarily found within 400 to 700nm—a range identified as photosynthetically active radiation (PAR). In a vertical farming environment, broad, white light has proven effective for tissue culture, propagation and vegetative growth—while also serving the more practical function of making it easier for human eyes to diagnose and observe crops day in and day out. As the body of research into LED applications has expanded, it’s become clear that lighting strategies need to shift based on growth stage. The days of bombarding plants with the same intensity and spectra are quickly fading. More and more research is showing that different cultivars respond to different lighting strategies at different stages of their maturation. More nuanced, customized lighting strategies are increasingly leading to tangible business outcomes for cultivators: longer shelf life, improved aesthetic, enhanced nutritional value, faster cycle times and higher yields.
LED improvements will continue to drive costs down, while more in-depth research will discover and confirm a new set of lighting strategies and operational best practices to help vertical farmers meet future market demand for increased food production while also improving profitability. Overall, the future for vertical farms is bright and ripe for even broader innovation. Automation—the final frontier of food production—will mean even greater control of agricultural environments. That future is on the horizon. For now, though, vertical farms just need to stick to what they can control, which is pretty much everything else.
About Abhay Thosar
Abhay Thosar is the director of horticulture services at Fluence by OSRAM, where he is responsible for managing a team of horticulture specialists that enhances how cultivators grow their crops, optimize their lighting strategies and increase profitability in their operations. He holds a Ph.D. in plant physiology from Gujarat Agricultural University and spent more than a decade at leading greenhouses and nurseries throughout the U.S.
The content & opinions in this article are the author’s and do not necessarily represent the views of AgriTechTomorrow
Comments (0)
This post does not have any comments. Be the first to leave a comment below.
Featured Product
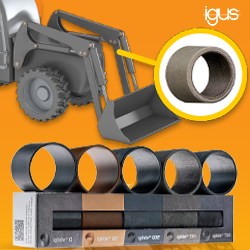