Digitized and automated processes are becoming increasingly important in modern agricultural enterprises. Machine vision methods play a key role here. Among other things, they can be used for a variety of precision farming applications.
Cultivating Farmland Precisely and as Needed
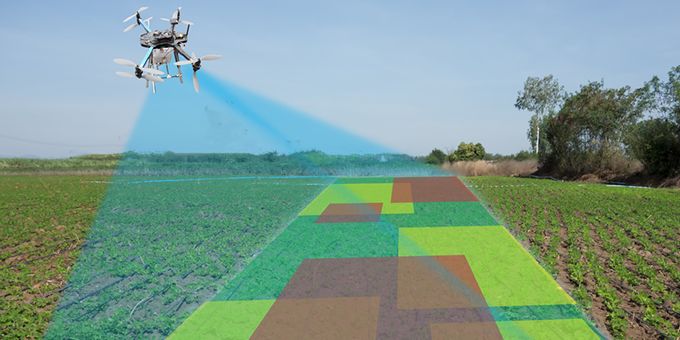
Article from | MVTec Software
To remain competitive, farmers must optimize their value-added processes and make them more efficient. Modern digital technologies that are used for intelligently automating workflows and adapting them to actual conditions (known as smart farming) offer practical support. Machine vision is gaining increasing importance in this context. Originating from industrial applications, it is now being used more and more in agriculture.
The technology consists of two main components: hardware and software. Hardware refers to what are known as image acquisition devices, such as cameras, scanners, and sensors, which first capture a large quantity of digital image data from specific scenarios in agricultural production processes. This information is then processed by machine vision software, such as MVTec HALCON, and made available for appropriate applications. For example, the system is capable of automatically recognizing specific objects and situations based on visual features alone.
Monitoring farmland using drones
Modern agricultural enterprises can make use of machine vision for the targeted and location-specific cultivation of agricultural acreage (precision farming). The following scenario demonstrates how this works in practice: A drone fitted with a high-resolution camera flies over a piece of farmland. The integrated machine vision software evaluates the recorded images and automatically detects certain features from the air. For example, an abnormal chlorophyll content in the crops indicates a fungal disease or pest infestation. Based on these findings, farmers can take highly targeted measures. For example, they can precisely spray only the affected areas with pesticides or fungicides. Multispectral processes integrated into the machine vision systems help determine the condition of the plants. Special multispectral cameras are used to detect and process additional color channels that are invisible to the naked eye. This allows abnormalities in the vegetation to be detected automatically, reliably, and at an early stage.
Another application scenario is targeted fertilization. In this case, the machine vision software precisely measures the crop height based on the digital image data, making it possible to fertilize only low-growth areas as needed. The same principle can also be used to irrigate fields on a location-specific basis. In this case, infrared cameras measure the temperature and create a heatmap of the relevant area. On this basis, the measured evaporation chill can be used to precisely determine the actual degree of moisture in the individual regions, so that irrigation can be specifically adapted to requirements. The image data does not necessarily have to be recorded by drones but can also be captured by satellites from a great height.
Conclusion
The use of machine vision technology provides farmers with all the benefits of precision farming. Agricultural land can be monitored, fertilized, and irrigated in a targeted manner, which makes for more efficient and sustainable cultivation practices. The optimized, need-based use of resources, including pesticides, water, and fertilizer, allows farmers to save money, reduce effort, and meet legal requirements more precisely.
The content & opinions in this article are the author’s and do not necessarily represent the views of AgriTechTomorrow
Comments (0)
This post does not have any comments. Be the first to leave a comment below.
Featured Product
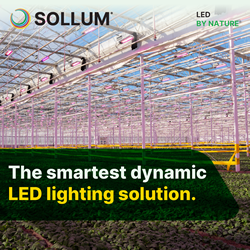