Robotics Plus unveils autonomous modular vehicle to alleviate agriculture labour shortages
FRESNO, Calif., and TAURANGA, NZ – Robotics Plus, a New Zealand-based agritech company, today launched its autonomous multi-use, modular vehicle platform for agriculture designed to carry out a variety of orchard and vineyard machine tasks - to alleviate ongoing labor shortages and transform the industry.
The multi-purpose Unmanned Ground Vehicle (UGV) can be supervised in a fleet of vehicles by a single human operator. The vehicle uses a combination of vision systems and other technologies to sense the environment - to optimize tasks and allow intelligent and targeted application of inputs such as sprays. Growers will be able to rotate multiple tools on the highly adaptable and configurable agriculture platform, depending on the day’s work - for jobs such as spraying, weed control, mulching, mowing and crop analysis.
Robotics Plus, a specialist in the design and build of robotics, artificial intelligence and autonomous machines, unveiled its demonstration vehicle at FIRA USA 2022, a California-based event dedicated to autonomous agriculture and agricultural robotics solutions for the North American market.
Steve Saunders, Co-founder and CEO of Robotics Plus, says its world-class team worked alongside growers, researchers and best-in-class technology suppliers to deliver the unique modular architecture for its multi-purpose UGV, which can operate in a range of environments.
“We’ve created a flexible agricultural platform with the power to adapt to different crop types with tools for various applications, providing year-round automation benefits and maximizing machine utilization.
“To adapt and thrive in a changing world and create a sustainable and competitive future in the agricultural and speciality tree crop sector - growers and orchardists need automation that solves real-world problems, reduces reliance on increasingly costly and hard-to-find machine operators and provides data-driven insights for informed decision-making.”
Saunders says that for automation to be adopted, it must also provide a good return on investment.
“Our multi-purpose vehicle replaces tractors and other tools. But, it does much more than just replacing labor – it’s loaded with intelligence to improve efficiencies,” he says.
The first application for the technology is intelligent spraying. The system intelligently varies the flow rate to ensure spray efficacy whilst reducing inputs. Spray rates and airspeed is controlled in zones and responds as the sprayer moves along orchard or vineyard rows.
The highly manoeuvrable UGV has a small footprint and unique steering configuration, incorporating electric steering and independent motors, which increases productivity - allowing significantly more ground to be covered than machines which turn on every second row or greater, depending on row configuration. The UGV can be deployed in a range of applications in various crop types with a minimum row spacing of 1.8M/6ft.
Dr Alistair Scarfe, Co-founder and CTO of Robotics Plus, says its hybrid electric diesel UGV delivers outstanding performance in the field.
“Electric drive motors give superior torque and control, whilst a Tier 4 diesel generator means the vehicle can operate for extended periods. Fuel consumption is minimized by electrically driving all systems, including tools. Regenerative braking and high-capacity batteries also extend efficiency and range.
“In addition, the vehicle’s lightweight design and intelligent all-wheel-drive system, with independent wheel motors to ensure grip and control - while significantly reducing ground compaction to protect the soil,” he says.
The vehicle has been designed from the ground up to be modular and easy to service. With no hydraulic, gearbox or differential fluids to be managed, operators can easily keep their vehicles running if a part fails by simply swapping out modules when needed. All of this is designed to reduce downtime and complexity for growers.
Robotics Plus has partnered with best-in-class technology suppliers, including Yamaha Motor Company, Autonomous Solutions Inc., and Croplands, to significantly increase the robustness and support for the product in a demanding environment such as agriculture.
Saunders says by taking a partnership approach, Robotics Plus has created a best-in-class platform for the agriculture industry.
“We’ve benefited from our partner’s deep knowledge and access to high-quality technology components. In addition, growers can deploy Quantum sprayers with configurations adaptable to various crop types, growing formats, and heights.”
Robotics Plus has developed multiple autonomous systems for use in agriculture and automation for intelligent fruit-packing to address significant industry issues, including global labor shortages, rising costs, and yield security. In addition, its robotic automatic log scaling machines are transforming port logistics with improved safety and productivity.
Robotics Plus’ fast-growing team developed the modular platform UGV at its Tauranga base, with extensive testing in New Zealand and the US in various environments and applications. Robotics Plus investors include Yamaha Motor Company and New Zealand’s ACC Impact Fund.
Robotics Plus’ new autonomous modular vehicle is available for pre-order. For more information, see https://www.roboticsplus.co.nz/
Comments (0)
This post does not have any comments. Be the first to leave a comment below.
Featured Product
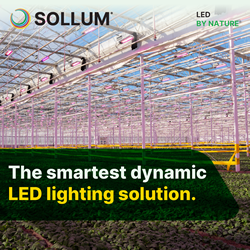