Work starts on world's largest vertical farm build from Jones Food Company
The new multi-million pound farm, being built in Lydney, Gloucestershire in western England, will offer 148,000 square feet of growing space.
It will be approximately the same size as almost seventy tennis courts and able to supply 1,000 tonnes plus of fresh produce to thousands of UK supermarkets, according to Founder James Lloyd-Jones.
He said: “With this new facility we further accelerate Britain’s position as a world-leader when it comes to vertical farming. We already supply thousands of British retail stores with basil grown in our first facility in Lincolnshire but this new site, which is three times bigger, will allow us to supply tens of thousands more stores and to widen our product offer with our partners.”
“Our food supply chain is under significant stress, with empty supermarket shelves and shortages of foods increasingly common place,” Mr Lloyd-Jones said. “Vertical farming is undoubtedly a vital part of the UK’s and the world’s farming future."
“Given what we’re already doing, the world-leading technology we have and the intensely pressing need for more sustainable forms of farming over coming decades, we plan to be able to supply 70 per cent of the UK’s fresh produce within the next 10 years."
“From an environmental perspective, vertical farming allows us to grow in 17 layers, so every acre becomes 17 times more productive. It allows us to grow entirely without pesticides and using 95 per cent less water. And it means we can significantly reduce the air and road miles of the foods we grow.
“But vertical farming doesn’t just make environmental sense, it makes economic sense too. Scale is vital in order to create a cost base that allows us to deliver delicious, healthy herbs, salad leaves, cut flowers, fruit and veg at a price the average shopper also really likes. This second facility further cements our ability to do this.”
“And this isn’t the end, we fully anticipate more facilities in other parts of country and around the world in coming years."
Lloyd-Jones said JFC believed, through the latest vertical farming technology, the so-called ‘garden of England’ could now grow in Cornwall, Gloucestershire, Yorkshire, Argyll, Fermanagh or pretty much any other county in the country, providing sustainable solutions for the UK’s food chain."
"We’ve learnt so much, had such strong backing and have such amazing technology that we now believe we can replicate and replicate and replicate," he said.
“I accept we’re currently a small part of the UK’s agriculture industry, but this move makes us mainstream, it makes us a really significant player in this country. And you only have to look at Germany, the Netherlands, the United States, across the Middle East and Asia to see this is a global movement, revolutionising the way the world grows produce – vertical farming is the future."
“Building the world’s biggest vertical farm puts the UK at the vanguard of this global movement – we’re leading the world’s vertical farming revolution."
Comments (0)
This post does not have any comments. Be the first to leave a comment below.
Featured Product
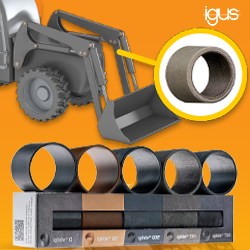