The initial results show that it is possible for tomato growers to maintain high levels of quality and production, even when they reduce the heat input in the greenhouse.
Trial Grodan and Philips Full LED shows high level quality tomato production with up to 40% heat input reduction
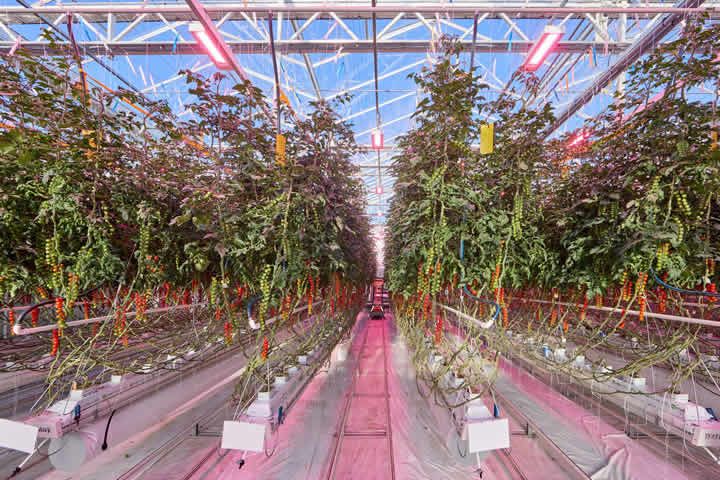
Case Study from | Signify
Against the backdrop of rising energy prices and the ongoing shift towards a sustainability mindset, Signify and Grodan are jointly conducting an innovative three-year research trial started in September 2023 at the Botany Research Centre in the Netherlands to optimise year-round tomato cultivation with the goal of achieving up to 40% lower heat input. Together with other partners in the industry (BASF Vegetable Seeds, Ridder, Normec Groen Agro-Control and Wireless value), Grodan and Signify are jointly organising knowledge transfer activities.
The initial results show that it is possible for tomato growers to maintain high levels of quality and production, even when they reduce the heat input in the greenhouse. When pursuing a precision-growing strategy, the growers can reach uniform and consistent results. Besides confirming the benefits of the fully dimmable Philips LED lighting and Grodan stone wool growing media in Controlled Environment Agriculture (CEA), the trial has already produced some surprising insights related to humidity management and the nutrition balance in the root zone.
Key trial findings
- It is possible to maintain high levels of uniform and consistent quality and production, even when heat input is reduced in the greenhouse.
- When growers manage humidity in the greenhouse with active dehumidification, they can minimise the impact of the lower radiant heat input (lower pipes, LED lights & increased screening hours) on the uptake of water and nutrients by the crop.
- Adapting the nutrient recipe, influences the growth habit of the crop and facilitates a lower energy input to the greenhouse.
- When controlling the water uptake, you can also precisely align the amount of water you give, helping you to further optimise water and nutrient input.
- By adjusting the nutrient recipes, especially nitrate and chloride levels, the leaf area index is positively influenced generating a more generative crop without adding extra heat.
Data-driven strategy
The strategy for the trial is founded on the knowledge gained from a previous successful tomato trial by Philips Horticulture LED Solutions. “And we’ve been building on that experience as we’ve progressed. Every decision we’ve made has been data-driven – from the initial cropping strategy, to the ongoing adjustments we’ve made to the plant density, the amount of LED lighting, temperature profile, and the irrigation moments,” emphasises Erik Stappers, Manager Plant Specialists Vegetable & Fruit at Philips Horticulture LED Solutions. “Because we can control when the lights go on and off, the intensity of the light and greenhouse humidity via active dehumidification it’s possible to calculate and plan the irrigation strategy very precisely.”
Driving transpiration to ensure nutrient uptake
The previous years research into low-energy growing focused on the climate strategy only, and the root zone has largely been ignored. But the climate influences the uptake from the root zone, and vice versa. If the radiant heat input into the greenhouse is too low, there’s a risk that the plant will not transpire sufficiently, meaning that the total nutrient uptake will be compromised. Therefore, to encourage sufficient plant transpiration an active air dehumidification unit was installed.
The use of the air dehumidification unit contributes to a more uniform greenhouse climate. Consequently, there is minimal variation in temperature and humidity values which can be seen from the numerous wireless sensors installed. Thanks to the air movement, there’s a very stable temperature profile, which makes it even easier to pursue a precision-growing strategy for uniform and consistent results.
“The dehumidification unit enables us to manipulate the 'pull' of transpiration rather than 'push' humidity into the greenhouse and this enables us to continually steer the crop towards optimum plant growth and development,” Andrew Lee, Knowledge Manager at Grodan mentions. “Thanks to our stone wool growing media we can use the GroSens root zone sensor data to closely monitor the changes in the root zone water content % (WC%) and EC. This enables us to precisely control and adapt the irrigation strategy.”
The biggest surprise has been the success of the air-dehumidification unit in maintaining a high level of transpiration. “The norm for HPS is usually 130 to 140ml of transpiration per mole of light, so at a 40% lower heat input we expected to see around 80 to 90ml. But in fact, based on the measured water content levels in the stone wool growing media, we are currently at around 100 to 110ml. This shows that if you actively manage the humidity, you can minimise the impact of the lower radiant heat input on the uptake of water and nutrients through the leaves.” Besides that, there was almost zero drain from planting in week 39 to first harvest in week 47. “Although that wasn’t our intention, it demonstrates that if you can control the water uptake, you can also precisely align the amount of water you give, helping you to further optimise water and nutrient input.”, Lee adds.
Active air dehumidification is a very suitable addition to low-energy growing. In fact, Lee and Stappers, wouldn’t be surprised if active air dehumidification and active control of the nutrient composition become standard commercial practice in a few years’ time.
Reduced nitrate levels
In parallel with the water and nutrient uptake, the trial is also exploring how adjusting the nutrient recipe, particularly nitrate and chloride levels can be used to influence plant morphology, particularly the leaf area index. Lee explains: “From an irrigation perspective, we’ve divided the compartment into two halves and are providing two different nutrient recipes in the same climate zone. The result was that in one half of the greenhouse we applied higher nitrate levels in the irrigation water. This created a crop with a leaf area index (LAI) of 2.5. Conversely, in the other half we applied a lower nitrate level (-30%) and created a crop with a LAI of 2.0. The result was a lower slab WC% by week 45 with higher nitrate levels as the higher LAI stimulated more transpiration from the crop. This meant that we were forced to give an additional irrigation moment, making the crop even more vegetative. This is a remarkable insight in terms of growing with a lower heat input, as traditionally vegetative crop development would mean increasing pipe temperatures. This has been a real eye-opener for the growers who’ve visited the trial greenhouse and they now recognise that by adjusting the nutrient recipe they can be more flexible with lowering the heat input.
Pushing the boundaries to advance sustainable agriculture
We aim to achieve 4.5 grams of fruit per mole of light in the winter period. “We’re excited to see that we have already achieved this at this early stage of the trial. With the help of our intelligent crop modelling tool CropSim that supports data-driven decisions based on the predicted fruit load, we’re pretty confident that we can tweak the parameters to improve this by a further 10%,” states Stappers.
In the meantime, the project partners will continue to gather data and fine-tune their approach. “More control and greater predictability across all aspects of plant development paves the way for more standardization and automation within greenhouses. Our ultimate aim with this trial is to develop a blueprint that guides tomato growers towards greater success in lowering heat input. We’re all very excited to be pushing the boundaries and creating new knowledge that is contributing to further advancements in sustainable horticulture,” concludes Stappers.
Sharing knowledge with the international community
The trial will continue until week 20 2024, when the ‘supplemental lighting season’ comes to an end. As part of our efforts to share knowledge, we will jointly be holding an end-of-season event on 24 April 2024. Growers and other members of the international high-tech greenhouse community will be invited to come and take a tour of the trial greenhouse, followed by a number of technical presentations in which we and our partners will present details of the key insights so far.
About Grodan
Grodan is the global leader in supplying soilless rootzone management solutions for Controlled Environment Agriculture. These solutions are applied to the cultivation of vegetables, medicinal crops and flowers. Grodan was founded in 1969 and is active in more than seventy countries worldwide. The head office is located in Roermond, the Netherlands. For more information, please visit www.grodan.com.
About Signify
Signify (Euronext: LIGHT) is the world leader in lighting for professionals, consumers and the Internet of Things. Our Philips products, Interact systems and data-enabled services, deliver business value and transform life in homes, buildings and public spaces. In 2023, we had sales of EUR 6.7 billion, approximately 32,000 employees and a presence in over 70 countries. We unlock the extraordinary potential of light for brighter lives and a better world. We have been in the Dow Jones Sustainability World Index since our IPO for seven consecutive years and have achieved the EcoVadis Platinum rating for four consecutive years, placing Signify in the top one percent of companies assessed. News from Signify can be found in the Newsroom, on X, LinkedIn and Instagram. Information for investors is located on the Investor Relations page.
The content & opinions in this article are the author’s and do not necessarily represent the views of AgriTechTomorrow
Comments (0)
This post does not have any comments. Be the first to leave a comment below.
Featured Product
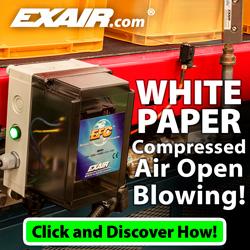