"Buying an LED installation is one thing; learning how to use it is another". After a long run-up, pot lily and pot chrysanthemum producer Van Schie started using two different LED installations in 2022 and 2023.
New Insights and Data-driven Controls Come Together in Priva Connext
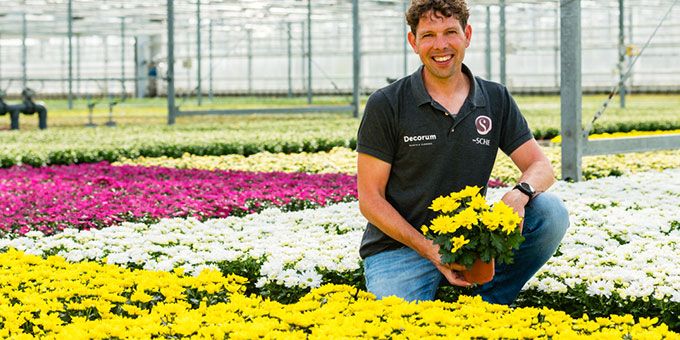
Case Study from | Priva
After a long run-up, pot lily and pot chrysanthemum producer Van Schie started using two different LED installations in 2022 and 2023. “Finding out how to integrate grow light, climate controls, and energy management in a smarter way is a continuous learning curve for us. The climate computer plays a key role. The controls in Priva Connext are therefore frequently updated and extended,” says co-owner Marcel van der Voort.
Marcel van der Voort has a passion for technology that helps him optimize and automate his business processes. “Our quest to find efficient grow light for our pot lilies started in 2015,” he reflects. “Full LED was on the rise, but we couldn’t make the numbers work at the time. By late 2020 the energy market was becoming more dynamic and the outlook was better. One year later we set up some trials to get a clearer picture.”
The trials took place in one compartment and consisted of HPS lighting (reference), HPS + LED, and full LED with red and blue light. “Looking back, we rushed things a bit,” admits Van der Voort. “We had no far-red light at the time, we didn’t prepare properly, and we had too little time and knowledge. It was a tough lesson, but thanks to the assistance we got from companies like the consultancy Ledgnd and Plant Lighting, in 2022 we were able to engage in more focused discussions with our partners, including Mechatronix, Priva, and Enthoven Installatietechniek. That gave us the courage to invest in full LED.”
Three pillars
The HPS setup in a 15,000 m2 compartment was completely replaced with dimmable, dual driver Mechatronix Coolstack LED lights (1000 W) with a maximum output of 110 µmol/m2/sec PAR (red, blue, and green (white)) with separately controllable far-red light. Van der Voort realized straight away that it would be several years before he could get optimal use out of the installation because of the other climate factors and the need for efficient energy management.
“Buying an LED installation is one thing; learning to use it is another,” the grower says. “What we are aiming for is data-driven growing. That is based on three pillars. The first consists of reliable data on the essential climate and growth factors. This data should give us the information we need to avoid damaging the plants. The Vivent biosensor offers us insight into plant stress so we can identify and eliminate the causes more quickly.”
Lighting and climate controls
The second pillar involves optimizing setpoints and controls in the climate computer to cope with the complex energy management. Van Schie is supported in the energy optimization process by AAB, while Priva consultants help to integrate his energy management into Priva Connext, where the lighting and climate controls are also configured. Van der Voort: “The recent update of the I-20 lighting strategy control opens up new options, such as modulating control of the LED lights or imitating sunrise and sunset. We will be making good use of those.”
The third pillar is a clear, real-time picture of crop growth. “We need to know how the plants respond to different light and climate conditions,” he explains. “We record that with Priva-Aranet sensors and the plant sensors.”
Marcel advises any grower working with full LED to use a plant temperature meter in combination with a net radiation meter to get an understanding of the radiation balance and plant temperature.
New trials and insights
In consultation with the knowledge partners involved, Van der Voort started a new series of trials in November 2022. These have already delivered new insights into the use of full LED in their pot lilies. “Adjusting up and down gently prevents plant stress, allowing the energy to be converted more effectively into growth,” the grower says. “A second lesson we have learned is that far-red light is beneficial and needs a separate control that doesn’t have to be synchronized with the red, blue, and white spectrum. Also, we now know that one night per 24-hour period is better for the plants than several rest times and that the plants don’t respond well to lighting periods of more than 17 hours. So all in all, thanks to the sensors the plants are teaching us how to optimize our LED settings.”
Marcel is using wireless climate and plant sensors to gain new insights into crop responses to changes in climate and light conditions.
Even more complex
This year, a second dimmable LED installation with a slightly higher lighting capacity, also from Mechatronix, followed. This is a triple driver system with 2 x 650 W and an output of 160 µmol/m2/sec. “One driver controls two lights on both sides,” Van der Voort explains. “This installation has an even more homogeneous light distribution and offers a 60% bigger field of light for optimizing the grow light than the first one. We can continuously adjust the red/blue, white, and far-red lights independently of one another. We think white light is only needed to provide good working conditions, so we will only be using that when and where people are working. It would be ideal if you could have the lights controlled by an electronic transmitter that the workers carry with them, but that isn’t possible yet. The entrepreneur is curious to find out how the plants respond to the additional short-term white light. “No doubt the biosensors will tell me,” he says.
Steering based on RTR
In the upcoming lighting season, the grower wants to steer the crop more specifically based on the RTR. “A higher temperature when solar radiation is high, a lower temperature when it’s low,” is how he summarizes the strategy. “This enables us to use heat more efficiently, screen more effectively, and boost the growth rate with additional lighting. This could make a difference of three weeks per crop compared with HPS and fixed heating curves.”
Van der Voort is convinced that wide-ranging integration of climate (including light) and energy management will deliver much more than the energy savings quoted. “Product quality will also improve,” he says decidedly. “We will be talking to the Priva consultants again soon to fine-tune the light and energy controls in Priva Connext. This will take us forward step by step, and we will continue to learn from each other. That is useful for everyone, as developments are happening in quick succession.”
The content & opinions in this article are the author’s and do not necessarily represent the views of AgriTechTomorrow
Comments (0)
This post does not have any comments. Be the first to leave a comment below.
Featured Product
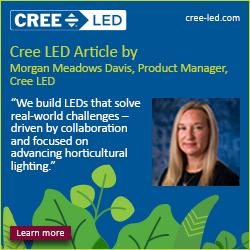