CEA is importantly not the answer to all the systemic problems in food production, but it is a powerful method that adds much needed resilience into supply chains, as the climate across the globe changes.
How Can Greenhouses, Vertical Farms & Container Farms Work Together?
Article from | LettUs GROW
Greenhouses, vertical farms and container farms are all different forms of indoor farming, also known as Controlled Environment Agriculture (CEA). As our climate grows increasingly hostile, and we wake up to the environmental cost of exporting produce across the globe, nations are turning to indoor farming in an effort to strengthen food networks and reduce their reliance on international exports.
It is no longer a case of will indoor farming technology be used to feed our ever growing population, but what form will it take. CEA is importantly not the answer to all the systemic problems in food production, but it is a powerful method that adds much needed resilience into supply chains, as the climate across the globe changes.
Commercial greenhouses, vertical farms and container farms are all going to be needed to help support our changing food supply system, and where they are best situated to work collaboratively with traditional farming practices is going to be a defining factor in their usage.
Automated commercial greenhouses
Positives: Extensive supply potential, less energy intensive, diverse crop portfolio
Considerations: Space required, level land, source of energy
Also referred to as “glasshouses”, commercial greenhouses are often viewed as the most traditional form of indoor farming. Automated commercial greenhouses operate using a single layer of crops positioned under a ceiling of glass, using a combination of natural sunlight and LED or halogen lights, allowing them to grow out of season and extend the growing hours of the day.
By supplementing the additional power needed for artificial lights with natural sunlight, greenhouse growers have the benefits of much lower energy footprints when compared to vertical farms, whilst still reaping the benefits of year round growing potential and reliable harvests. Greenhouse growers are however not exempt from the instability of the energy market, and will need to consider carefully where they are sourcing the power needed to grow the vast quantities of produce they are capable of. Commercial greenhouses are particularly suitable for utilising low-grade biomass waste-heat and CO2 capture from industrial sites to supplement their energy, so feasibility studies should be conducted to assess potential local sources.
Growers can use soil, hydroponics and even aeroponics to fertilise and irrigate their produce, allowing growers a range of options to diversify their crop selection. Depending on the irrigation method, greenhouse growers can harvest crops such as tomatoes, strawberries, leafy greens and herbs all year round, and have even found success growing vanilla pods, which have become increasingly threatened by tropical storms and deforestation in Madagascar, which supplies 85% of the world's vanilla.
Due to the expansive size, controlled environments and year round growing potential, commercial greenhouse facilities are able to greatly exceed crop yields found in conventional agricultural operations, and supply vast regions with steady supplies of fresh and healthy food.
One important aspect to remember is that greenhouses need large amounts of space. Greenhouses typically run in hectares, not metres, so having the land to accommodate a large-scale set-up is key. For this reason, densely populated urban locations are unsuitable for major greenhouse constructions, as are areas with sloping hills and uneven ground.

Vertical farms
Positives: Year round harvest, less space required, suitable for urban and rural locations
Considerations: Source of energy, energy consumption, suitable crop selection
Vertical farms are becoming far more common in agriculture than they were a decade ago. Crops are grown in densely packed shelving which span the length and breadth of warehouses or underground growing facilities, with LED lights acting as the sunlight, and irrigation from hydroponics or aeroponics used to supply the nutrients and the water.
With the use of LEDs comes the added need for power, and it will likely be the largest output in any indoor farming business model. Accessing low-carbon energy sources or building dedicated biomass or solar solutions to feed vertical farms will be a must-have addition to make sure crops are not only cost-effective for the consumer, but that carbon emissions associated are also reduced..
The advantage of vertical farming facilities is that they provide increased production capacity of fresh produce, without spanning the same land-mass as commercial greenhouse facilities. Vertical farms can supply urban cities and rural towns with ease, and if situated correctly can help supply surrounding areas too.
Although they are not suitable for larger, towering crops such as tomatoes and green beans, vertical farmers can specialise in fast growing, nutrient rich salad leaves, micro greens and berries which are much shorter in height and can be supplied throughout the seasons.
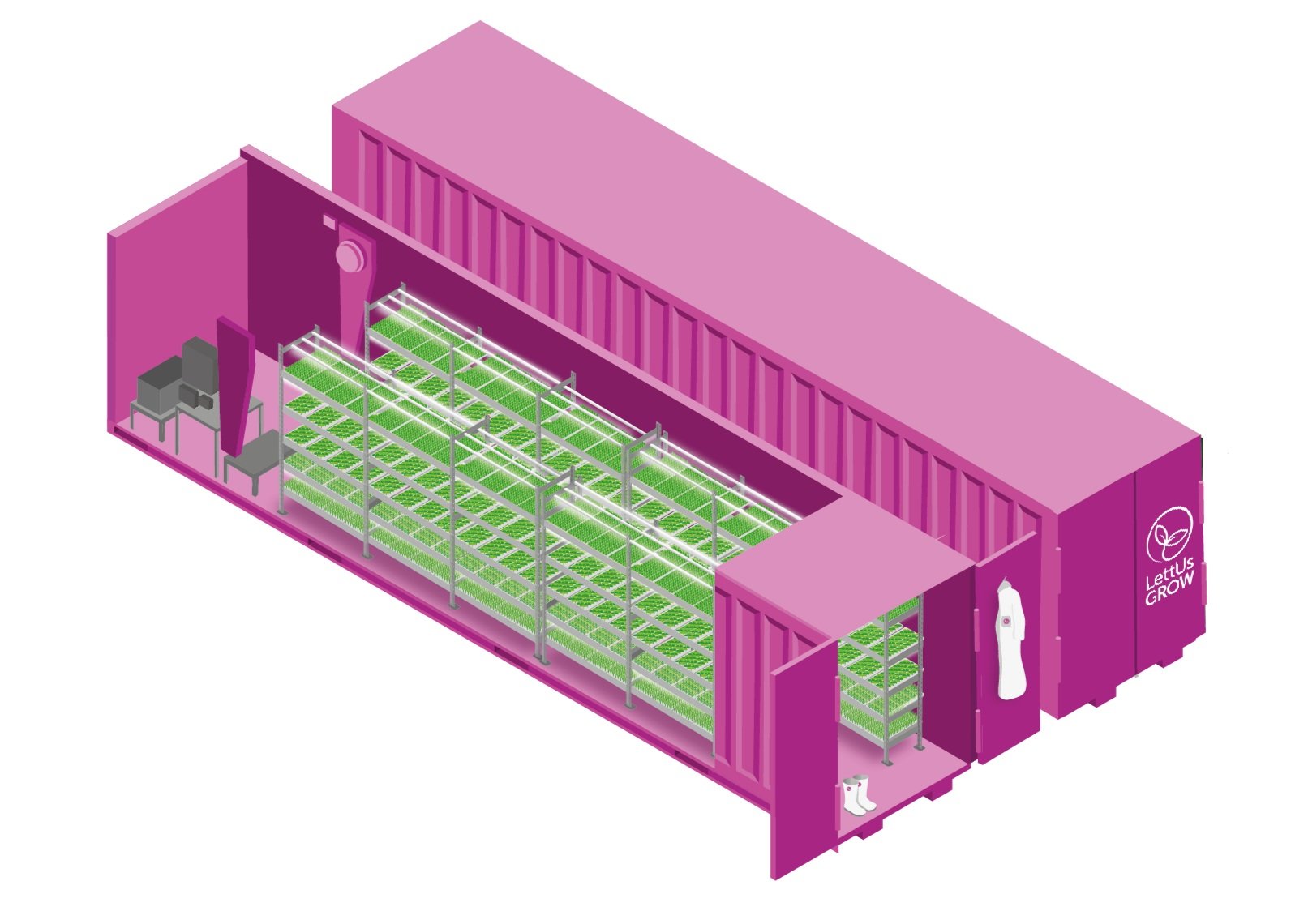
Container farms
Positives: Year round harvest, easily transported, modular
Considerations: Source of energy, serves smaller areas, manually operated
Unlike the permanent structures needed for greenhouses and vertical farms, container farms are a flexible, scalable indoor farming option, and are easily transportable throughout the UK and the globe. Standing at 40ft in length, DROP & GROW containers are neatly adaptable for both busy city centres, or in rural communities.
Unlike greenhouses which require hectares of land and potentially years of property development, containers require only a flat surface, access to power and water for a community farm to be set-up and operate effectively. Container farms are best used when there is limited space, or if growers are looking to gradually expand the business - they can simply add containers to create a multi-tainer set-up, without having to find a new location with every expansion. This is also useful if growers are temporarily leasing the land, and intend to relocate - with no planning permission required, containers can be rapidly redeployed, leaving farmers the flexibility to re-establish themselves in more favourable locations.
The reselling of container farms is also fairly uncomplicated when compared to vertical farms and greenhouse facilities. Combining farming technology inside a transportable shipping container means the whole farm can be sold as a whole without finding separate buyers for the machinery, parts and decommissioning the area.
The added and immeasurable benefits of container farms lies in their ability to provide a unique access to education and community engagement. Urban neighbourhoods and communities that are disconnected from the food system instantly have access to a working farm, providing fresh healthy food which has been grown and harvested on their doorstep. Aeroponic containers provide a brilliant tool for education, and most recently rehabilitation, where users can gain experience in aeroponic plant husbandry and build new skills in a rapidly growing sector of agriculture.
Much like vertical farms, energy supply is a major consideration when looking to set-up your own container farming business. Containers do not have the advantage of vertical farms where systems can be automated and they are operating on a much larger scale, so they can see a higher cost per kilogram of produce. Container growers should be paying particular attention to their energy usage, and if possible should use farm management software to monitor the largest sources of energy such as lighting, irrigation and the environment and make adjustments remotely.
If you are looking for advice on how to source sustainable energy solutions, make sure you read our blog in partnership with District Eating, which shares advice on what energy solutions to consider when setting up your own container farming business.
What is the future for controlled environment agriculture?
There is no doubt traditional farming will continue to be a prevalent part of our society. We will still see rippling fields of wheat, rapeseed and barley rolling throughout the countryside, with apple harvests and pumpkin picking in the autumn before the winter frosts set in. Greenhouses, vertical farms and container set-ups are not here to replace conventional agriculture - however, we will need throughout the years to supplement our food supplies, and rebuild the certainty we’re losing in our weather patterns, workforce and supply chains.
By using the right indoor farming solution in the areas where it will reap the most positive benefit, controlled environment agriculture can work alongside traditional farming practices to provide both the stability and predictability growers of all backgrounds relish, and we all require to stabilise our food supply into the future.
The content & opinions in this article are the author’s and do not necessarily represent the views of AgriTechTomorrow
Comments (0)
This post does not have any comments. Be the first to leave a comment below.
Featured Product
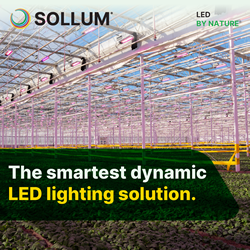