When owners and head growers first start thinking about building a new commercial grow facility, often the first thing on their minds is profitability—how do we differentiate our product and outperform the competition with better plant quality and higher yields?
Do's & Don'ts of Commercial Grow Facility Design
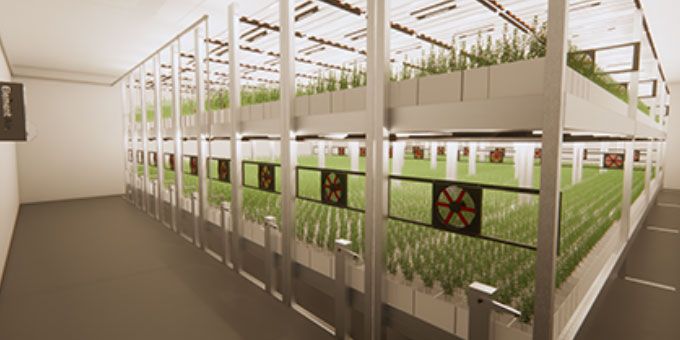
Article from | urban-gro
In the same way that high-performance plants start with exceptional seeds, high-performance buildings start with early-stage design engagement. Without the right infrastructure and systems integration necessary for efficient facility operation defined during the design stage, you can count on change orders impacting your budget during construction as modifications and updates stack up.
Starting off with purpose-driven design equips your team with the tools and understanding needed to get to market quickly and outperform the competition.
In this blog, we’ll break down a few Dos and Don'ts for commercial grow facility design.
Getting Started: The Guts of the Grow
So you’re ready to make the leap into commercial cultivation and one of the first key considerations is related to the building. Will you retrofit an existing facility or build something new from the ground up? And more importantly, what’s it going to cost? The reality is that many growers can't afford to build from the ground up (or simply don’t want to) because it can take two to three years to even get the permitting for a new build approved—and that's before even breaking ground. Leasing or purchasing a pre-zoned building is generally much quicker and can serve to buy you time if later you decide to scale your operation with a ground-up build.
What about the height of the building? Is bigger better? When it comes to vertical space, more height can be better. Higher ceilings allow for more lighting and multi-tiered growing areas. However, more height can also be a lot more complicated due to the prevalence of microclimates and the need to mitigate them in order to support healthy crops. Active monitoring and a purpose-designed HVAC system are the only ways to ensure uniform growth in a multi-tiered system.
Grow Facility Build-Out
Once you have a building or site it’s time to consider what goes into a commercial grow facility build-out. You will need to hire an architect, a general contractor, an environmental engineer, a structural engineer, a mechanical engineer, and that's before you even start to work with equipment suppliers. Managing all of these different contractors and consultants can be a huge drain on your time, not to mention frustrating and confusing. Instead, many growers opt to go with an architect-led, turn-key design-build partner. Regardless of whether you’re designing a new facility, working in an existing building, or expanding operations, having a single point-of-contact throughout the entire design, construction, and commissioning process saves abundant time and headache.
Systems & Equipment
The systems and equipment outfitting your facility will be integral to your success and yield major implications to the overall efficiency and profitability of the facility. While full automation isn't always financially feasible or right for every facility, you should be monitoring key environmental conditions and metrics to ensure a healthy crop. Temperature, vapor pressure differential (VPD), and airflow are all key to high-yielding plants. Lighting is perhaps the single system with the largest impact on overall facility efficiency and upfront CAPEX. LED lighting systems will give you more efficient lighting with a wider spectrum, but the upfront costs are higher than that of HPS fixtures.
Working with a consultant to help you evaluate the costs/benefits of your lighting will help you choose the best style for your grow. Another major system with important facility impacts is benching. Oftentimes, benching selection is left until nearly the end of the project which is a mistake. It’s important to determine which cultivation racks you want to use early in the design process. Will you go single or multi-tier? Fixed or rolling? Your benching layout, combined with the footprint of your facility, will dictate your total canopy square footage which is integral in projecting future yields.
Team and Tech
Building Your Dream Team
One of the most critical factors affecting your success is your team. From consultants to your head grower, building a strong team at the outset will help you avoid common pitfalls and stay on top of the competition. When evaluating contractors and partners, look for firms with controlled environment ag (CEA) experience. Not just any commercial building contractor will do—building an office building is nothing like building a grow facility. Save yourself from making the mistakes of those that came before you by working with a firm.
Leveraging Ag Tech for Healthy Plants
As outlined in the previous section, a commercial grow facility relies on dozens of systems and pieces of equipment to run smoothly. To design a successful commercial grow facility, you will need to use specialized grow lighting, irrigation/fertigation equipment, an HVAC system, benching/racking systems, and that’s just the tip of the iceberg. Beyond that, integration of these systems is critical to growing plants and profits. You can have top-of-the-line systems throughout your facility, but if those systems aren’t working together—or worse, they’re working against one another—it’s all for naught.
While the technology needs of a commercial grow can be daunting, it's important to lock down tech choices early so the design/construction phases don’t lag behind.
What is the best commercial grow room HVAC design?
There is no single best HVAC design—each system will vary based on your specific conditions. But make no mistake, an HVAC system is the lungs of the operation, and is the key to consistency in grow environments. It's also one of the largest investments you’ll make in your operation, so you want to get it right.
In the grow room, air sanitation systems can work with your HVAC equipment to reduce both airborne and surface contaminants like bacteria, mold, and other pathogens that will infect your plants and wreck your yields if given a chance.
VPD, or Vapor Pressure Deficit, refers to the vapor pressure inside a plant as compared to the air pressure outside the plant. A well-controlled VPD can give you less stressed plants with improved CO2 absorption, and higher yields. A poorly managed VPD can result in disappointing yields and wasted resources.
Enterprise-level grow facility designs have specific HVAC requirements. Plants will need effective airflow distribution to prevent microclimate development and to maintain consistent VPD. Leaf temperatures should also be maintained at an ideal level, preventing large fluctuations. Last, but certainly not least, the relative humidity must be kept stable and within a narrow range—which will change at each stage of plant development.
Knowing where to start with HVAC design can be overwhelming, but an experienced mechanical engineer and consultant can get you on the right track. If you are ready to design a commercial grow facility that will put you ahead of the competition, contact urban-gro today to talk about starting your design.
The content & opinions in this article are the author’s and do not necessarily represent the views of AgriTechTomorrow
Comments (0)
This post does not have any comments. Be the first to leave a comment below.
Featured Product
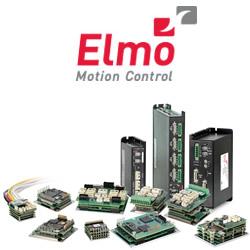