Engineers working in the agricultural industry can benefit greatly from implementing true maintenance- free pivots within their machinery. Maintenance-free pivots have several benefits that can help significantly increase efficiency within the agricultural field.
Designing a True Maintenance-free Pivot
White Paper from | igus
Engineers working in the agricultural industry can benefit greatly from implementing true maintenance- free pivots within their machinery. Maintenance-free pivots have several benefits that can help significantly increase efficiency within the agricultural field. Here, we will compare true maintenance-free designs with alternative designs, as well as go into the requirements for creating a true maintenance-free pivot.
Legacy Designs
Unlike true maintenance-free designs, legacy designs require substantial downtime. Thus, legacy designs aren’t typically considered ideal. Legacy designs are composed of:
-
Metallic bushing with grease grooves
-
Steel housing with grease zerks
-
Steel pin, sometimes hardened depending on the application
Disadvantages:
-
Continuous maintenance (sometimes daily) for the end user
-
The cost of grease and replacement parts if not performed regularly is very expensive, i.e.: the pin, bushing, or housing
-
External lubrication is required, which attracts dirt and debris from the surrounding environment and creates a sand paper effect on the bushing and pin
Traditional Maintenance-Free Designs
Traditional maintenance-free designs are a better alternative than legacy designs, but they are not as effective as true maintenance-free designs. The traditional maintenance-free design is not a true maintenance-free design because only one critical aspect of a maintenance-free pivot, the bushing, is utilized. Traditional maintenance-free designs are composed of:
-
Dry running, self-lubricating bushing, i.e.: igus® iglide® (polymer), rolled metallic with Teflon lining, or fiber wound
-
Steel housing without grease zerk
-
Steel pin, sometimes hardened depending on the application, as well as a thin layer of a corrosion inhibiting substance (zinc, nickel or hard chrome)
Disadvantages:
-
Corrosion protection for the housing is removed
-
The pin becomes a secondary wear surface due to the poor corrosion inhibitor
-
Less expensive manufacturing costs, but a higher total cost of ownership due to the need to eventually replace the bushing, pin, and housing
By the removing grease used for lubrication, you have inadvertently introduced two critical issues that will cause premature failure in an application:
Results of a housing without corrosion protection
-
There is no corrosion protection for the housing.
-
Corrosion will begin to form almost immediately on the inner portion, where there is no bushing material. This corrosion will flake off and begin to prematurely wear both the bushing and pin simultaneously.
-
Corrosion will begin to form between the outer diameter of the bushing and the inner diameter of the housing, which will cause the housing to shrink around the bushing. Doing this will reduce the clearance between the bushing and pin, and increase friction and the wear rate of the bushing.
-
The pin will deteriorate at a higher rate due to the absence of an effective corrosion inhibitor.
-
Commonly used corrosion inhibitors, such as zinc, nickel, and chrome, are very thin layers applied to a pin and are quickly worn off during normal operation.
-
Once the inhibitor is removed, the base alloy gets exposed to the environment and the surface finish will become much rougher than any plain bushing can successfully run on.
-
This corrosion and degradation of the surface finish may be unnoticeable during continuous operation. However, once the machine is idle for any length of time, the corrosion will be able to expand rapidly, and in some instances, cause the pivot to seize altogether.
Result of using a thin, ineffective corrosion inhibitor on a shaft after only one season
True Maintenance-Free Designs
A true maintenance-free design must incorporate three features:
iglide® plain bearing
GKF shafting for a walking tandem pivot on a cultivator
-
The use of an igus® iglide® dry-running, self-lubricating and maintenance- free bushing: iglide® bushings are built for long service life and are low in cost. They require no external lubrication, and thus little to no maintenance. iglide® bushings are injection molded from a blend of thermoplastic materials, embedded reinforcing fibers and solid lubricant. The fiber reinforced materials make the bushings strong and resistant to high forces and edge loads, and the solid lubricants help lower the coefficient of friction. They also have a low wear rate, substantial chemical resistance, quiet operation, high load capacity and the ability to operate in extreme temperatures. Additionally, they are dirt, dust, UV and corrosion resistant. iglide® bushings always offer a solution, either from the catalog range or as a custom-made solution.
-
A synthetic wax-based corrosion inhibitor used to protect the housing bore: This is the most overlooked aspect of a maintenance-free pivot. Not only does it protect the housing from corrosion, but it also assists in maintaining a press fit for the bushing.
-
A cost effective, high quality, corrosion resistant pin with GKF Shafting: With GKF shafting, you are able to utilize both a hardened and a corrosion resistant pin. The hardness can be comparable to hard chrome when using the correct base alloy. Also, the corrosion resistance is roughly 3-5 times better than zinc, nickel, or chrome plating. igus® performed salt spray testing in accordance with ASTM B117-16 requirements and achieved 300 hours without any signs of red rust on the main body of the pin. The corrosion- resistant layer is very difficult to wear past since it diffuses into the surface of the pin. The pin would need to suffer roughly 0.020mm of wear in order to penetrate past the inhibitor layer.
Advantages:
a. Significantly lower total cost of ownership for the owner/operator
-
Very little downtime due to routine maintenance of the individual pivot
-
The bushing only has to be replaced once a threshold of acceptable clearance between the bushing and pin is achieved
b. The bushing becomes the wear surface and sacrificial portion of the pivot, which is the true design and purpose of a bushing
c. The housing, by design, should not need replacing during the normal lifetime of the unit
To read the white paper click here.
The content & opinions in this article are the author’s and do not necessarily represent the views of AgriTechTomorrow
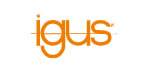
igus
In agricultural applications, solutions that can stand up to rough conditions such as dirt, dust, heat, shock and edge loads are essential. Igus makes this possible with its cable carriers and plastic bearings that are characterized by their outstanding resilience and long service life. These products can be used in tractors, disc harrows, fertilizers, field sprayers, and other agricultural equipment. In many applications, metallic bushings or recirculating ball bearing guides can be replaced by self-lubricating polymer plain bearings to not only improve technology, but significantly reduce costs as well.
Other Articles
igutex® bearing range vs bronze bearings
What is the best plain bearing for agricultural machinery?
New Tool Eases Vine Pull - Tractor-Mounted Toolbar Digs Into Job at Lower Cost Than Skid Steers
More about igus
Comments (0)
This post does not have any comments. Be the first to leave a comment below.
Featured Product
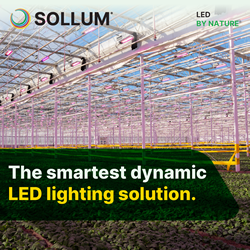