At one time solely being known as the jewel in the summer salad, the role of the tomato has now evolved into something much bigger – potentially game-changing, in fact. Could it be about to solve the global food crisis? At least, one greenhouse in Holland thinks so.
Is the Future Tomato Red?
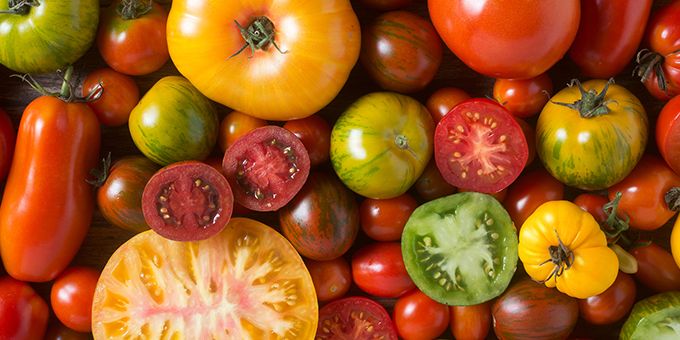
Article from | Light Science Technologies
With around 7,500 types in the world, it’s fair to say that the number of tomato varieties surpasses that of Heinz baked beans by some stretch.
At one time solely being known as the jewel in the summer salad, the role of the tomato has now evolved into something much bigger – potentially game-changing, in fact. Could it be about to solve the global food crisis? At least, one greenhouse in Holland thinks so.
The HQ of Duijvestijn Tomaten – which translates to Duijvestijn Tomatoes – sits on a mammoth 25-hectare site containing several imposing greenhouses which are 12 metres in height and hundreds of metres across.
From here, an annual 17 million kilograms of tomatoes are harvested from 12ft high plants every April. Using hydroponics, the company produces 20 times as many tomatoes per square metre as a field in Spain. Within a mere 48 hours, they’ll be sitting on a shelf at a Sainsbury’s near you.
“A field in Spain will yield roughly four kilograms of tomatoes per square metre per growing season,’ says Ernst van den Ende, a professor at Wageningen University, a school that has helped shape Dutch success, and who ran its Plant Sciences group for 12 years. “In a top greenhouse in the Netherlands, that same square metre will produce 80 kilograms of tomatoes.’ The UK has more or less caught up.
This is all happening amid what is an extremely precarious situation for global food supply, with Russia’s invasion of Ukraine again exposing its weakness and complexity.
The impact on grain supplies, as well as disruption to natural gas and fertiliser markets are having widespread, possibly long-lasting consequences. We’re now seeing shortages of cooking oils in British supermarkets, with other foodstuffs likely to be hit. This isn’t the only factor. It is an unwelcome addition to the growing list of problems on a global scale, including soaring energy prices, droughts and climate change. All are collectively wreaking havoc on the food supply chain, as the world is tasked with the urgent need to feed 10 billion people over the next century.
It’s not all doom and gloom. A recent study has highlighted why indoor wheat farming may be the saviour, although we still have some way to go until this comes to fruition. The answer lies in hi-tech solutions, and the benefits of AgTech innovation are becoming clearer through growing crops such as tomatoes. Use of LEDs is also helping to reduce energy usage, while other tech such as AI may offer the chance for plants to be monitored individually.
One leading AgTech specialist (ahem!) in the UK is paying particularly close attention to ways in which it can reduce energy costs while growing vine crops with the aim of championing crop production using technology. Working in conjunction with Crop Health and Protection (CHAP), its six-month tomato trial at Stockbridge Technology Centre’s advanced glasshouse facility is testing low power technology through trialling three different light combinations to see which produces the most yield for the least energy.
In the meantime, while we await the outcome and reflect on the potential this small fruit of wonder holds, we’ll celebrate all things tomatoey.
The content & opinions in this article are the author’s and do not necessarily represent the views of AgriTechTomorrow
Comments (0)
This post does not have any comments. Be the first to leave a comment below.
Featured Product
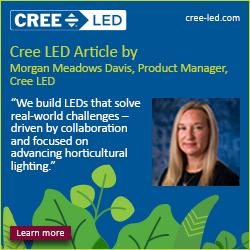