Every week is harvest season in Western-designed hybrid farm
The Agrotunnel is an indoor growing system that can produce berries year-round. (L to R) Food Security Structures president & CEO Kim Parker, Agrotunnel operations manager Amita Sharma, Food Security Structures vice-president & chief technology officer Greg Whiteside, John M. Thompson Chair in Information Technology and Innovation Joshua Peace and graduate student Max Qian. (Kathryn Hollinrake for the Weston Family Foundation)
Climate change and severe weather are the primary challenges facing year-round berry production in Canada. Western University professor Joshua Pearce and the Free Appropriate Sustainable Technology (FAST) research group have devised a food security solution to address these global threats by developing a net zero energy farm, which extends the growing season of berries and greatly exceeds average Canadian yields.
Currently in its first full year of operation at the Environmental Sciences Western Field Station, the Western-led project combines a photovoltaic (solar panel) shielded outdoor farm with an Agrotunnel, which is an indoor growing system that houses high-density vertical aeroponic (growing plants in the air) and hydroponic (growing plants in water) hybrid systems that use high-efficiency, spectrally optimized LED grow lights.
The Agrotunnel, provided by industry partner Food Security Structures Canada, and the agrivoltaic farm – one that combines solar energy and crop production – are supported, in part, by a $1 million grant from the second phase of the Homegrown Innovation Challenge, funded and supported by the Weston Family Foundation.
“Our solution provides an extremely high-density, resilient method to obtain year-round healthy fruit and vegetables at a minimum production cost,” said Pearce, the John M. Thompson Chair in Information Technology and Innovation at Western Engineering and Ivey Business School. “The system is completely modular, scalable and adaptable to various locations and extreme climate conditions.”
The year-round farming system, as conceived, can be attached to retail locations like grocery stores to provide zero-mile food supply, nearly anywhere in Canada.
Joshua Pearce at the Environmental Sciences Western Field Station with a solar photovoltaic array. (Kathryn Hollinrake for the Weston Family Foundation)
Following last year’s testing, Pearce and the team have experimental evidence that the Agrotunnel works physically to produce year-round berries, but the economics can be a challenge depending on the location because of electricity costs.
“Every week in the Agrotunnel, harvest season is upon us, and the future of Canadian farming is ripe with possibility,” said Pearce.
To improve the economics, and decrease, or even eliminate, the electricity costs, the Agrotunnel and surrounding area at the field station are covered with adjustable partially transparent solar photovoltaic arrays, which were designed by Pearce and his team. The agrivoltaic arrays, a series of solar panels, are part of the Western Innovation for Renewable Energy Deployment (WIRED) experimental testbed. All of the WIRED designs are completely open-source hardware and use some 3D-printed parts, both tantamount to many of Pearce’s engineering projects.
Agrivoltaics is a portmanteau of ‘agriculture’ and ‘photovoltaics.’ While harnessing solar energy, the arrays are also used as shields to protect the outdoor plants from extreme weather, creating a microclimate to conserve water while providing all the electricity needed to run the lights, water pumps and heat pumps (used for heating and cooling) inside the Agrotunnel.
The strawberries, blueberries, honeyberries, gooseberries, boysenberries and others grown at the field station are monitored with artificial intelligence, including computer vision systems, to monitor moisture, carbon dioxide levels and high energy efficiency. The berries are also tested in agrivoltaics systems under different strengths of solar cells to find optimal conditions for outdoor growth as compared to indoors.
‘Light’ bulb moment
Boosting food productivity and power by optimizing the use of sunlight addresses a wicked problem in Canada and around the world. If the project delivers the way it is expected to, the impact on global food security is limitless.
“Our moveable Agrotunnel, Better Grow Lights and aeroponic/hydroponic growing system, combined with Dr. Pearce’s unique agrivoltaics system, creates an energy efficient, climate-controlled growing space that can handle severe climate and Canadian weather,” said Kim Parker, president and CEO of Food Security Structures Canada. “This project addresses food insecurity by empowering individuals and communities to grow their own food locally, year-round, regardless of climate or location.”
Food Security Structures Canada Agrotunnel. (Kathryn Hollinrake for the Weston Family Foundation)
Launched in 2022 by the Weston Family Foundation, the Shepherd phase of the Homegrown Innovation Challenge awarded $1 million each to 11 research teams to develop ideas for extending the growing season of berries. Each team only has 18 months to build and test its proof-of-concept ideas before the next phase of the challenge, which will see this group of 11 reduced to four teams.
“At the heart of this competition lies the belief that the fusion of collaboration and broad expertise is the key to solving complex challenges in agriculture,” said Garfield Mitchell, Weston Family Foundation chair. “Our grantees bring out-of-the-box, yet achievable, ideas to the table, and we are excited to see the innovations that arise from their shared passion and collaboration.”
Comments (0)
This post does not have any comments. Be the first to leave a comment below.
Featured Product
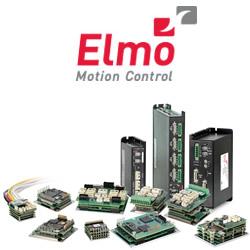