NORD DRIVESYSTEMS Delivers Efficient, Economical Solutions for End-of-Line Packaging
The use of decentralized drive solutions with asynchronous motors can achieve cost benefits of up to 50% while providing a more compact footprint and high-efficiency operation.
End-of-line packaging processes can include heavy loads, high forces, and long travel distances. While drives with centrally controlled servo motors are commonly used in these applications, they are not always required for applications such as palletizing, stabilizing, and handling. For these systems, decentralized drive solutions with asynchronous motors are a more efficient and cost-effective option. NORD DRIVESYSTEMS is highly familiar with the packaging industry's specific requirements and has developed specialized solutions for end-of-line packaging applications.
Thanks to their high inertia, NORD asynchronous motors offer decisive advantages for end-of-line packaging systems. The motors are widely available in power ranges from 0.16 - 75.0 hp and are made for use with NORD's full line of gear units and variable frequency drives. When it comes to moving heavy loads, asynchronous motors deliver a higher level of control and movement than conventional servo solutions that require adjustment to the application via large gear ratios. They also provide higher process stability, quiet operation, and reduce vibrations along with risk of damaging the loads or packaging machines.
NORD's decentralized variable frequency drive options include the NORDAC BASE, NORDAC FLEX, NORDAC LINK, and NORDAC ON/ON+. These electronic control products can efficiently control conveyor speeds, manage individual product placement and pickup, and smoothly operate palletizing machines without slowing product flow. Along with their high performance, NORD VFDs offer flexibility as the modular design concept allows changes and maintenance to take place at any time without large structural modifications, extensive downtimes, or changes within a control cabinet. The decentralized solution also saves on space as the VFDs can be directly mounted to the motor without need of a full control cabinet setup or extensive wiring system.
Depending on the system type and application, NORD decentralized variable frequency drives paired with asynchronous motors can amount up to 50% savings compared to the legacy design. The high efficiency of asynchronous motors work to lower operating costs and reduce the number of system variants - saving money and storage space. The motors not only lower procurement costs, but also include a greater selection of options, wider availability, and simplified maintenance.
To download the white paper and learn more about NORD's solutions for end-of-line packaging industry, visit: https://www.nord.com/us/campaign/industries/end-of-line-packaging.jsp
Featured Product
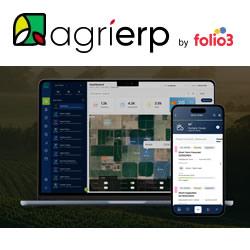