Robotic ‘harvesting as a service’ proves cost-effective in trials by fieldwork robotics
Trials show ‘cost per kilo’ equivalent to human labour
As about 30% of the UK raspberry crop lies rotting in the fields, the need for automating the delicate harvesting operation becomes more acute. Fieldwork Robotics has developed a robotic raspberry harvester, and the Cambridge-based company is running trials with selected growers on a harvesting as a service basis.
Rui Andres, CEO of Fieldwork Robotics, presented at the REAP 2021 Start-Up Showcase. He says quality and cost per kilo of fruit picked are the most important factors when harvesting raspberries, rather than speed alone.
"The KTN has estimated that the UK is short of 90,000 pickers, and this not only means a waste of the crop but also limits the potential for growth.
"We are aiming to complement the human workforce with a robot harvester that will operate for longer hours. This will free staff for quality control and other skilled jobs and create the opportunity to use more of the crop for other products.
Fieldwork Robotics, a spin-out from the University of Plymouth, has developed a variable-stiffness robot arm that emulates some of the aspects of the movements of a human arm, with the control and grippers required to capture a delicate object and handle it sensitively. The system is easily reconfigurable to other fruit, vegetables and delicate objects by simply changing the grippers.
"We have made huge progress over the last year rationalising the design to provide a simpler, more robust solution with fewer motors and moving parts," says Rui. "The product is an automated soft fruit harvester, designed for working in polytunnels and greenhouses alongside humans."
The company is on track to deliver an automated harvester that will be available to harvest on a pay-per-kilo basis and is currently fundraising to speed its development.
Rui continues: "We are aiming to raise £5m in this year's funding round to begin commercial manufacture in 2022. We are currently able to manufacture small batches, but the next step is to optimise the product for the assembly line.
"We need to start providing this service as soon as possible to allow all of the crop to be harvested - that's hugely important for the grower to reduce the risk. If we don't step in, there is a lot of wastage, and growers will be forced to shut their doors."
Featured Product
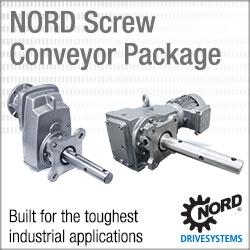
NORD IE5+ Motors: Highest Gearmotor Efficiency in a Compact Design
NORD gear units, motors, and electronic control products focus on durability, adaptability, and high efficiency for a wide range of manufacturing applications with over 20,000,000 standard configuration options. Featuring IE5+ PMS motors that can work effectively at partial loads and low speeds thanks to their constant torque and high overload capacity. Their smooth surface and ventilated designs provide ultimate versatility and variant reduction. Combined with surface protection options, such as IP69k or NORD's state-of-the-art nsd tupH Sealed Surface Conversion System, NORD drives are ready to take on the demands of extreme manufacturing environments.