To reduce this loss and ensure that harvested grain remains fresh and undamaged, the ongoing monitoring of the storage environment is essential. As such, farms and storage operators are turning to advanced monitoring technologies, with sensors placed in silo towers.
Advances in carbon dioxide IoT sensors enables the reduction of grain wastage in silo bags
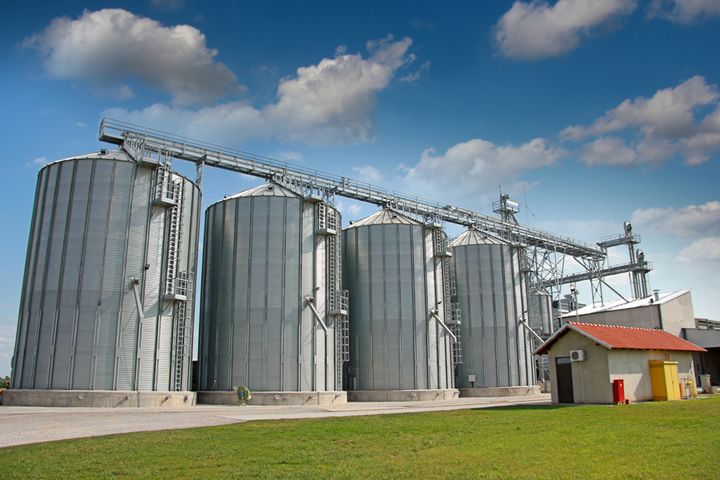
Neill Ricketts, Chair | GSS
Grain wastage remains a significant challenge in agriculture, with substantial losses occurring during harvesting, processing, and storage. According to the Food and Agriculture Organization (FAO), post-harvest grain losses can range from 10 to 20 percent globally.
Losses are attributed to factors such as improper drying and inadequate storage conditions which result in microbial activity and pest infestations, as well as respiration from the grain itself. To reduce this loss and ensure that harvested grain remains fresh and undamaged, the ongoing monitoring of the storage environment is essential. As such, farms and storage operators are turning to advanced monitoring technologies, with sensors placed in silo towers.
In addition to silo towers, silo bags are often used as a practical, more flexible solution for storing harvested grain directly in the field, eliminating the need (and cost) of transporting it. These are made from UV-resistant polyethylene, and are sealed to create an anaerobic (low oxygen) environment, which naturally helps reduce pest and microbial activity.
However, despite the anaerobic conditions, pest infestations, microbial activity and grain respiration can still occur and monitoring the internal conditions of these silo bags remains crucial to maintain grain quality and prevent spoilage.
IoT detection methods
Despite the problem being caused by raised temperatures and moisture levels, among the most accurate early warning indicators is a rise in CO2 concentrations within the silo bags. CO2 is produced through the metabolization of carbohydrates in the grain by fungi, bacteria insects and other unwanted pests and is therefore a strong correlative early-warning indicator of grain deterioration that enables details inspections to be made - such as for moisture, temperature hotspots, pest activity and damage to the bag - and the required action taken - from repair to disposal to prevent further contamination.
Under normal conditions, CO₂ is a stable and largely non-reactive gas and therefore is difficult to detect using simple electrochemical methods. However, CO2 does absorb light at specific wavelengths, in its case the mid-infrared (IR) wavelength of 4.25 µm and this allows the creation of IoT sensors for CO2.
The problem with doing using this method for IoT sensors is power. Gas sensors have traditionally used incandescent IR light sources to illuminate and measure the absorption spectrum of a gas and therefore understand the concentrations of each gas present (see figure 1).
Fig 2: Airborne substances can be identified by their absorption of IR at specific wavelengths with CO2 absorbing at 4.25 µm.
However, these incandescent sensors require significant levels of power to operate, and this has limited their use to mains powered IoT equipment only.
This is suitable for use in silo towers, but silo bags are sealed, requiring the use of batteries. And crops such as cereals or pulses are stored for 12 to 18 months, with the battery (practicably) unchangeable during this period.
The move away from broad-bandwidth incandescent NDIR emitters, and their replacement with narrow-spectrum solid-state NDIR LEDs and emitters has delivered significant power efficiency improvements, as well as an increase in their mean time to failure. But, even with these gains, the power consumption is typically in the region of 50 to 150 mW average, with a peak of 300-400 mW.
This is still far too high, meaning battery-powered IoT systems are limited only to short-term use.
Alterations in the sensor and system design enable greater efficiency savings
1) Duty cycle
The sensor’s biggest power drain is the light source. Reading frequency is therefore critical.
At this point it should be noted that, unlike carbon monoxide or radon, there is no danger to life from the buildup of carbon dioxide inside the silo bags and we do not therefore need to undertake a duty cycle several times per second. Sensors can be set to run at far less frequent intervals.
CO2 rises will occur slowly within the bag, and a duty cycle of one reading every 10-15 minutes will enable power consumption to be brought down significantly.
2) Processing
The next biggest power drain is the energy required by the MCU to process readings. Here, the optimisation of signal processing algorithms used by the sensor enables efficiency gains to be made here through. It is also possible to implement of measures (especially hardware) that further reduce computational loads.
Additionally, it is crucial to look at the power used during stand by and sleep modes, with measures implemented to reduce this as well as the incorporation of more energy-efficient components elsewhere on the board.
Combined, these elements can make it is possible to create a more efficient CO2 sensor.
As an example, by implementing these measures, the GSS CozIR-Blink NDIR CO2 sensor is able to runs at sub 1.5 mW levels and with a peak of c.33 mW, requiring just 60 µJ per reading, while delivering an accuracy of 30ppm.
IoT system development
Fig 3: A schematic for an IoT CO2 sensor for use in air quality monitoring. Switching to the new generation of low-power CO2 sensors, with an appropriately set duty cycle, would enable this to run for years before batteries are replaced.
Looking to the system as a whole, a wireless CO2 monitor suitable for use in silo bags needs to consists of four major building blocks. As listed above the first two are the sensor and microcontroller, with these joined by a low power radio module and power source (see fig 3).
Sensor: As we’ve highlighted, advanced sensors can run at 60 µJ per cycle, with just four to six cycles per hour.
The processor: A microcontroller with a low power design and exceptionally-low-power sleep mode will be needed and a good example of this is the STM32L0 from ST Micro.
Wireless data transmission protocol: For this, LoRaWAN is arguably the best suited protocol as it can be both exceptionally power efficient yet can transmit over the very large area of a farm without the need for multiple routers.
And this leaves the power source. The above combination of components within an IoT system will be able to run for several years when powered by an AA battery, which is well beyond even the longest grain storage need.
The content & opinions in this article are the author’s and do not necessarily represent the views of AgriTechTomorrow
Comments (0)
This post does not have any comments. Be the first to leave a comment below.
Featured Product
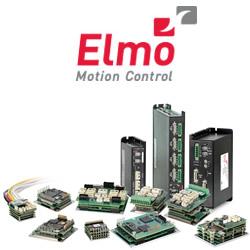