amBX spoke with Stephan den Boer from Bever Innovations on their podcast about the role of technology in vertical farms, the challenges and opportunities faced.
Challenges and Opportunities Faced in Vertical Farming
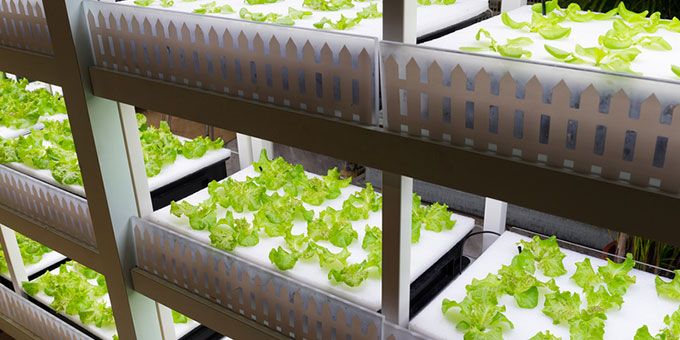
Q&A with Stephan den Boer | Bever Innovations
Vertical farms are heavily reliant on smart technology, data insight and precise control to grow quality crops.
amBX spoke with Stephan den Boer from Bever Innovations on their podcast about the role of technology in vertical farms, the challenges and opportunities faced as well as tips to optimise operations and improve results.
Bever Innovations are known as an innovator in the LED lighting industry, they have been established since 1996, and they operate in multiple application areas, including indoor farming.
Below are some key highlights from the conversation. To listen to the episode in full, click here.
What is a vertical farm, and why is it important?
”In my opinion, a vertical farm is an indoor environment where you're trying to recreate the outdoor circumstances (e.g. the daylight spectrum is 400 to 700nm). And why would you do that? Because the outdoor environment is not always suitable for certain crops, e.g., in the Middle East, it’s hard to grow certain crops efficiently.
Local to local is important from an environmental perspective; locally produced and locally distributed produce is in demand.
We have completed projects in Japan for lettuce, and customers are willing to pay higher prices for fresh produce there because there is more limited availability than in the likes of the UK or Holland. You can influence the taste and colour when something like lettuce is grown in a vertical farm and enhance the crop to produce higher quality products for the consumer, all without pesticides or any chemicals being used in the process”.
How important is precise, granular control of light in this environment?
“In a vertical farm, you’re trying to create the best conditions for your specific crop. Lighting is an integral part of the process because, without light, the crop would not grow. Vertical farms do not have exposure to daylight because you want to be able to control the circumstances as much as possible. This means using a climate chamber to recreate the perfect circumstances each time.
You can continue to tweak the circumstances for as long as you like and still get new and better results. There are people who have been working in this field for over 20 years, exploring and researching the best possible light colours, humidity, temperature, irrigation conditions, etc. All factors are important; it’s the combination of them all that really makes the difference”.
What is the benefit of a vertical farm?
“Growing crops traditionally means that you're always dependent on the weather; even if you grow in a greenhouse, adverse weather conditions are still a factor. With indoor farming, weather conditions and seasons have no impact, so you're actually trying to create the perfect circumstances to get the maximum yield”.
What is the cost of setting up a vertical farm?
“I think the initial cost of a vertical farm where you have a fully controlled environment (CEA) is always higher. You can go for more low-tech solutions to keep the cost down, but the level of investment is always going to be relatively high, and the more data and control, the better the conditions and, therefore, higher quality yields are produced.
Some crops are a bit pickier than others, so consideration has to be given to what kind of crops you are planning to grow in your vertical farm. You have to make a suitable business case for the investment. However, with that being said, it is a predictable model. You’re collecting data to create an environment that you know is going to be perfect; this can be replicated time after time, and little intervention is needed unless customer demand changes”.
What is the biggest challenge faced in vertical farming?
“I think integration is a major challenge; it is important to work together to make sure all vendors’ technology can communicate, create the best environment and allow data to be utilised effectively.
I think collecting data, drawing conclusions and then learning from that with other companies is a vital part.
Getting companies to integrate their technologies into one platform, collecting all the data and sharing knowledge for others to use is the main opportunity because no matter how hard you try, one company by itself is never going to achieve it all”.
How energy efficient are vertical farms?
“If you make a 1-to-1 comparison between vertical farms and traditional farming, then it's always going to be better to get your energy from the sun. But realistically, we're getting into a situation where that is not a possibility all the time anymore. Climate change is happening, there’s limited space, and people have to live somewhere.
In terms of efficiency and consumption, it might be higher in a vertical farm, but the yields might be higher too. It's a comparison that is very difficult to make; obviously, the energy from the sun is free, so using solar panels and other forms of renewable energy should be incorporated to make vertical farms more sustainable, but if we want to have locally produced food, which is pesticide free, I think it's the only way to feed ourselves in the future.
You can also look at hybrid models. I think they’re sometimes a bit overlooked. I don’t think traditional growers should quit and start vertical farming, but they could consider moving some of their crops indoors. For example, we have customers who are trying to save space in their greenhouses, and they have decided to move their young plants indoors instead of doing it on tables all spread out, they’re now using multilayer systems to grow their young plants in a much more efficient way, and they’re getting much better results”.
amBX’s multi-protocol communication allows data to be aggregated and displayed in a central source. Their system monitors lighting as well as Co2, humidity, temperature and other factors. The custom dashboard displays information in a user-friendly format, or normalised data can be sent to a third party, the cloud or another system. Discover more here.
The content & opinions in this article are the author’s and do not necessarily represent the views of AgriTechTomorrow
Comments (0)
This post does not have any comments. Be the first to leave a comment below.
Featured Product
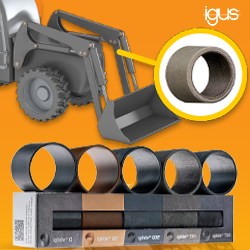