52% of commercial growers reported using LEDs as of 2020–an increase from 25% in 2016. This trend is expected to continue in the next decade. The sharp rise in LED-use among commercial growers is really two-fold: energy savings and complete optimization.
Switching Up Indoors – Why Growers World-wide Are Upgrading to LEDs
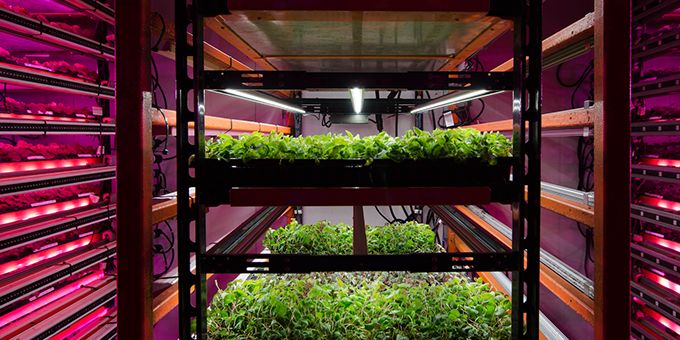
Article from | FLUENCE by OSRAM
52% of commercial growers reported using LEDs as of 2020–an increase from 25% in 2016. This trend is expected to continue in the next decade. The sharp rise in LED-use among commercial growers is really two-fold: energy savings and complete optimization.
Early adopters of light-emitting diodes tended to focus on how much energy LEDs would save compared to the once-standard high intensity discharge (HID) lighting. Now, in addition to reducing operating expenses (OpEx), growers are using LEDs to push light intensities, to maximize production within their existing facilities, and to exert further environment control.
Regarding energy efficiency, commercial LED fixtures achieve 2.6 micromoles of photosynthetic photon flux (PPF) per joule of electricity over their service life–compared to HPS fixtures that average 1.9 micromoles per joule. Furthermore, LEDs cut out most of the maintenance and replacement costs that legacy systems incur. These immediate and valuable cost savings began the upward trend of LED installation and use.
But this trend promises to continue its sharp rise because LEDs do more than save costs–they increase revenue!
According to studies, a 1% increase in photosynthetically active radiation (PAR) corresponds to a 1% increase in harvestable product up to light levels of 1,500+ µmol/m2/s. In simplest terms, depending on environmental control, increasing PAR with LEDs by 15% generally results in a 15% increase in crop weight. The additional revenue gained by improving production and crop quality can outweigh the savings achieved by upgrading to LEDs–a fact that has become clear to commercial growers world-wide.
Beyond savings and earnings, LEDs present the greatest opportunities to exert environmental control indoors. The primary difference between LED and HPS systems is efficacy: LEDs produce more light and less heat with the same electrical input, which allows for thermal stability. By converting more electrical energy into light, LEDs reduce the total heat delivered into the growing space. So, as LED lights turn on and off, the room does not experience as much variability in thermal input, temperature, or relative humidity (RH).
When one considers savings, earnings, and added control, it becomes easy to see why so many growers are upgrading to LEDs. You can view the full Indoor Retrofit Guide or contact the experts at Fluence for more information about upgrading to Fluence LED solutions.
The content & opinions in this article are the author’s and do not necessarily represent the views of AgriTechTomorrow
Comments (0)
This post does not have any comments. Be the first to leave a comment below.
Featured Product
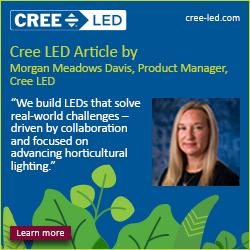