Each industry has additional standards that must be followed. For example, earth moving equipment used in mining has additional standards than a harvester in an agricultural setting.
Challenges of Developing a Safety System for an Agricultural Site
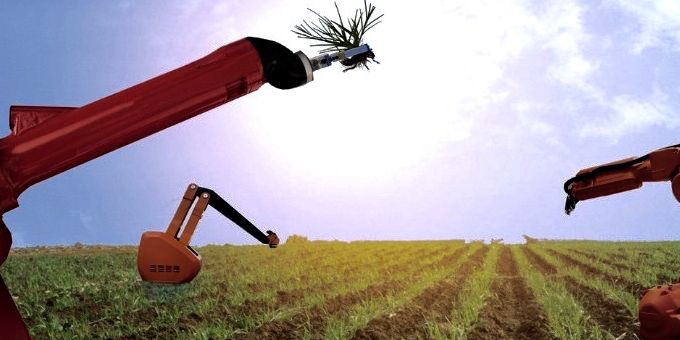
Q&A with Nathan Bivans, CTO | Fort Robotics
Tell us about yourself and role at FORT Robotics. 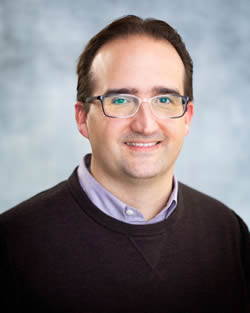
I'm Nathan Bivans, CTO for FORT Robotics. FORT started at the end of 2018 from another startup where I was also CTO - Humanistic Robotics Inc (HRI) and developed and patented a wireless safety protocol designed for dangerous applications in landmine clearance. From working with these big, dangerous machines at HRI, we realized the critical need for wireless safety for any robotic or autonomous machine. FORT’s mission is to enable the acceleration of autonomy by reducing risk and building trust in smart machines.
What are the challenges of developing a safety system for an agricultural work site, or one where there may be a mix of mobile machines and fixed machines and humans?
Agriculture is an early adopter of robotics and automation versus other industries. Obviously, with a growing world population (they say we’ll have to feed 10 billion humans by 2050), there is a clear need to have more food, but there's a labor shortage, and there's also a desire to protect the environment. And with commercial farming, you have thousands of acres of fields and crops to tend. Innovation is coming at a faster pace with autonomous harvesting machines, and machines that can detect weeds from crops and spray only the weed, smaller bots that use phenotypes and that travel through the rows to crops to sample soil and gather data about the farm. This precision farming is really turning the whole industry around and will ultimately help feed the world, and allow farmers to focus on the operational side of their business to be more productive and profitable.
What standards exist today, and are they being well-understood and followed?
The standards for functional safety with robotic and automation systems have a common base regardless of industry. However, each industry has additional standards that must be followed. For example, earth-moving equipment used in mining has additional standards than a harvester in an agricultural setting. Likewise, within construction, material handling vehicles have an additional set of standards than an excavator. Standards is a broad field with specifics to each industry, and manufacturers are starting to get a good handle on them.
What do you think the biggest barrier is for companies to commercially deploy agricultural robots at scale?
TThere is a range of barriers based on the type of worksite where robots are. Robots are moving beyond closed or fenced environments where there are likely limited risks. To scale big, companies will want to have open and collaborative environments, where humans are alongside these machines but doing more interesting work, and supervising the machines doing the dull and dangerous work. But, one of the biggest barriers to overcome to get there is that level (or the lack) of trust between humans and the machines. Without trust of the machines, people will not work in those environments, or license robotic systems for their worksite if the robotic system is not certified safe and secure. To gain trust, there needs to be a foundation and philosophy of safety and security built-in to the robot development. There also should be 3rd-party certification. A big delay in deployment might be caused once projects move beyond prototypes and into real-world environments and organizations have to go back to the drawing board because they don’t have the proper 3rd-party certification or followed the recommended standards. As well, price is going to be a factor - for the big commercial farmers it may be less so, but for the medium-small farming operations, the costs for autonomous equipment need to come down. And of course, everyone working on a farm wants the confidence and trust that the autonomous machines and robots are safe and won't cause physical harm to them, crops or other high-value assets. Another potential barrier is integration into existing equipment – it has to be easy, otherwise, robots won't scale as fast as they could.
Tell us about FORT and how your company helps companies solve these challenges?
At FORT, our background for many of us stemmed from developing robotics for land-mine clearance equipment, and we know first-hand how essential the functional safety requirements are for these huge machines. We spun out that aspect - safety technology for robotics - when we formed FORT at the end of 2018. We fine-tuned our wireless safety first in the form of a E-stop button (emergency stop) and a rugged, lightweight remote control with integrated Estop that allows workers to maneuver big machines from a safe distance and out of harm's way. Our next-gen platform is built on these principles and brings greater flexibility and advanced features. We've worked with hundreds of customers around the world and listened to their needs and concerns they face to accelerate their deployment. We’ve learned that overall risk needs to be mitigated, and buyers and end users of autonomous machines are demanding proof systems are functionally safe and secure at the endpoints.
At FORT our solutions quantify safety; we have provable and repeatable processes that are 3rd-party certified. In our development of wireless safety, we recognized the requirements for security. Because these machines are or will be connected to the Internet to gather and send data, employ telematics, track preventive maintenance, etc - the risks are massive. If a hacker, nefarious party, or disgruntled employee gets inside even one of these connected machines, they can wreak a spectrum of havoc across an entire fleet. You can imagine the consequences if one of these big machines gets hacked into, from causing damage to crops, injuring humans, and stealing data. It only takes one incident to lose trust, not to mention the hundreds of thousands or millions of dollars in loss of productivity and revenue. You can't be safe if you're not secure, and our hardware-based security is integrated with our certified wireless safety as a holistic approach.
At a big commercial farm, the machines can be mostly autonomous - this is definitely happening now with harvesters. But there is a need for workers to be able to maneuver these autonomous machines in and out of areas (ex: barns), for maintenance, for example. The FORT system allows users to maneuver those machines with our Remote Control and in a safety-rated way, then switch the machine back to its onboard autonomous mode and the safety features on the machine take over (lidar, sensors, etc). In addition, our system can be used for short- and long-range applications. As autonomy becomes more prevalent in farming, it will be critical to be able to safely stop a machine from a tele-operations control center or work trailer miles away.
What do you think the progression will be for commercial scale of agricultural robots over the next 2-5-10 years?
Full autonomy is still a ways out in part because of the complexity of implementing certified wireless safety and endpoint security measures. We've had automation in factories and manufacturing for decades, and eventually the fences will come down. But for new areas like construction and agriculture for example, we will see more tele-operations, data analytics, and remote control use in the next 2-5 years, and in 10 years perhaps a mixed fleet of semi- and fully-autonomous equipment working with humans on a job site. Another big hurdle to commercially scale robots is the level of autonomy that can be achieved with current technologies. Most systems are "trained" using gigabytes of information collected over time to develop learning sets (this is where Machine Learning plays a big role). The reason most systems haven't reached the highest levels is due to the unpredictability of the world around them. The main factor for unpredictability is human behavior, which is not predetermined or controlled by an electronic system that's tied into an autonomous system. So, in essence, the pace is governed by our ability to reduce the inherent risk of machines being around people. If we can provide a higher level of safety, we can hasten the arrival of robots in everyday life.
The content & opinions in this article are the author’s and do not necessarily represent the views of AgriTechTomorrow
Comments (0)
This post does not have any comments. Be the first to leave a comment below.
Featured Product
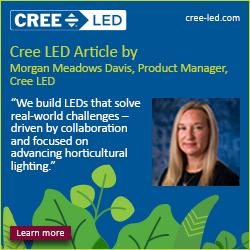