Though a pump can fail due to age and use, the reality is that most are murdered, snatched from their prime with much life left in them. The culprit is cavitation and it sends warning signs but most are ignored.
Imploding Concern: Identifying Destructive Pump Cavitation
Ray T. Bohacz | Farm Machinery Digest
There are many pumps found on the farm and each one is critical in its own way. It differs little if it is the coolant (water) pump on an engine, a hydraulic system or any other application; a broken pump can bring your entire farm operation to a standstill.
Though a pump can fail due to age and use, the reality is that most are murdered, snatched from their prime with much life left in them. The culprit is cavitation and it sends warning signs but most are ignored. I think we all experienced a pump vibrating excessively, hammering, groaning and whistling. If so, you witnessed pump cavitation.
Defining cavitation
Pump cavitation describes the formation of bubbles or cavities in the bulk fluid being moved that usually develops around a low-pressure area.
This is the result of either an entrained gas in the liquid from the vapor pressure being exceeded or from a lack of flow.
When the vapor bubbles collapse or implode, they strike at the speed of sound, creating noise and vibration. This collision will erode the surfaces of the pump and impeller while the harmonic attacks the bearing, shaft alignment, and seal. The pump is destroying itself during cavitation.
When a failed pump is examined you will notice an appearance that resembles a sponge-like texture or missing material.
Depending on the pump design and operating characteristics the bearing may fall victim first, allowing excessive shaft movement and a collision of the impeller with the housing.
Minor cavitation will result in decreased output or pressure. It is imperative that you are cognizant of the sound and pressure/flow characteristic of all the pumps in use on your fam.
Cavitation caught in the early stages will have minimal to no impact on pump life. The damage is done over time.
Two types of cavitation
Suction side cavitation occurs when a pump is under low pressure or excessive vacuum. The pump is being starved of liquid and is not being fed enough flow. At that time bubbles will form at the eye of the impeller (where it connects to the shaft). As the bubbles move over to the discharge region, the fluid condition is altered and the bubbles are compressed into a liquid, causing them to implode against the face of the impeller. An impeller that has witnessed suction side cavitation will have pieces of material missing.
Discharge cavitation is the result of the discharge pressure being extremely high, so that it is difficult for the liquid to vacate the pump. It then circulates around the impeller and housing causing a very high vacuum at the wall and the formation of bubbles.
In similar fashion to suction cavitation, discharge cavitation allows the imploding bubbles to create intense shockwaves, removing material from the housing and impeller. In extreme discharge cavitation cases the impeller shaft may even break.
Eliminating cavitation
The most common cause is a flow restriction or running the pump at a speed that is out of its operating range.
The flow issue can be either on the suction or pressure side, or a cumulative effect of both.
Proper and timely maintenance of filters and screens go a long way to prevent cavitation.
A sprayer or other application with old and weathered rubber hoses can be experiencing a slight collapsing of the lines and thus, limit suction performance while evoking cavitation.
Plumbing design parameters such as pipe diameter and the amount of turns and the sharpness of them will potentially create either suction or discharge cavitation. You may have upgraded to a larger pump and now the factory piping cannot support it.
Every fluid does not like to make turns and will result in a flow restriction, both on the feed and discharge sides.
If a pump does fail you need to take it apart and determine if it was the result of cavitation. If there is a problem in the fluid system that is left uncorrected, then the new pump will eventually fail for the same reason. If material is missing or has pin holes, cavitation was occurring.
On an engine the coolant (water) pump seal can fail prematurely if the rpm is brought too high while the thermostat is closed. During that time the coolant is being forced through a small bypass hose or passage.
Excessive engine speed even under no load will cause the suction side of the pump to experience a very high vacuum and over time, violate the pump seal and cause it to leak from the weep hole.
The engine rpm should be moderated when the coolant is below the temperature of the thermostat opening point.
The content & opinions in this article are the author’s and do not necessarily represent the views of AgriTechTomorrow
Comments (0)
This post does not have any comments. Be the first to leave a comment below.
Featured Product
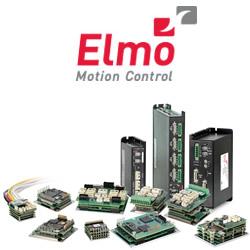