Getting a reliable structure with the right growing equipment is a good start, but to truly optimize their greenhouse, commercial growers need to incorporate automation.
The Benefits of an Automated Greenhouse in Commercial Growing
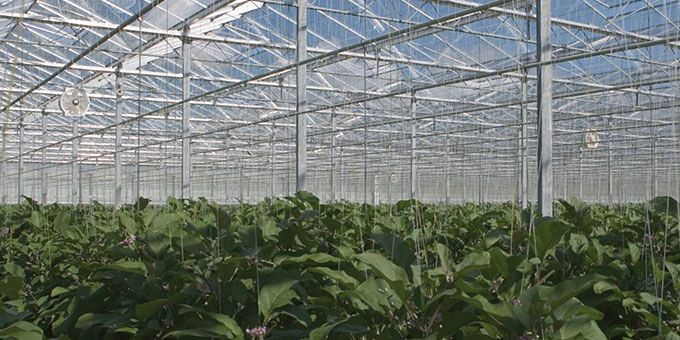
Article from | GrowSpan
Success in commercial growing comes down to one objective: growing the highest-quality crops at the lowest overall cost. This goal is a driving factor behind almost every operation’s decision-making process, as they try to outperform competitors and create a growing space that’s as efficient as possible.
Although the idea is simple, bringing it to fruition can be a challenge for growers. Without the right tools in place, commercial crop production can be cost and labor-intensive, and operations aren’t able to achieve the quality of harvests they need to sustain long-term success.
Getting a reliable structure with the right growing equipment is a good start, but to truly optimize their greenhouse, commercial growers need to incorporate automation. An automated greenhouse allows them to streamline nearly every aspect of their production space and gain precision control over growing conditions.
Although growers will benefit from any greenhouse automation system, they have the most to gain from regulating their irrigation, lighting and temperature. When operations run that equipment through an environmental controller as well, they can produce high-quality crops on even the largest scale, while also decreasing waste, labor and energy requirements.
STARTING WITH AN ENVIRONMENTAL CONTROLLER
When commercial growers plan on bringing automation into their greenhouse structure, they first need to think about how they’re going to manage the different systems. An environmental controller offers an ideal solution, because it allows them to tie all of their equipment together and manage growing conditions through one interface.
Advanced controller models can include up to eight or nine outputs, meaning they are capable of monitoring nine different automated systems at once. This includes everything from temperature and humidity control to lighting, CO2 enrichment, irrigation, fertigation and more.
If growers want to gain total influence over their production space, while further mitigating labor requirements and inefficiencies, they can implement a smart controller. Smart controllers will monitor an automated greenhouse around the clock, collecting information and using it to make on-demand modifications to the environment. This tool enables growers to create a fully automated smart greenhouse that maximizes profit potential, practically on its own.
WHAT IS A SMART GREENHOUSE?
A smart greenhouse takes advantage of a smart controller and other sensors to automatically regulate growing conditions. The controllers used in these greenhouses can react to changes in the environment and make adjustments on their own in real time, helping to maintain an operation’s ideal microclimate.
These automated controllers typically employ portable control panels or can be managed through a phone application. As a result, growers can monitor their automated greenhouse from almost anywhere to ensure everything is working at it’s supposed to.
When equipped with smart technology, an automated greenhouse may give growers the opportunity to collect and utilize data. Data collection allows operations to store a backlog of information that helps them make continuous improvements to their growing strategy. For instance, they can try replicating the same environmental conditions after an exceptional harvest, or make changes if their output wasn’t optimal.
BOOSTING CROP GROWTH AND LIMITING COSTS THROUGH PRECISION CONTROL
Once growers have chosen their ideal controller, they can integrate it into their structure and begin programming equipment. They’ll be able to tailor the automated greenhouse around the specific needs of their crops, giving them a dependable microclimate where they can flourish.
This will not only promote major improvements in crop growth, but also help operations save money by limiting labor, energy consumption and wasted resources. Three elements of crop production that will provide the most benefits in an automated greenhouse are irrigation, lighting and temperature control.
IRRIGATION MANAGEMENT
By automating their irrigation system, growers can put crops on an optimal watering schedule, which will help encourage uniform development and faster growth rates. This should also keep them from having to tend to their setup daily and prevent excess water usage, limiting waste and reducing monthly watering costs.
In addition to promoting more robust growth and decreasing waste, automated irrigation can assist with keeping potential inhibitors at bay, like pests and disease. With a precise watering schedule, potted systems are more likely to retain ideal soil moisture levels, stopping root rot and other common issues from occurring. Similarly, this will help keep hydroponics setups clean and properly aerated to encourage healthy root development.
EFFICIENT LIGHTING
Supplemental lighting requirements are influenced by different factors, like the type of crop being grown, the time of year and the amount of sunlight available to growers, so automation is crucial for maintaining optimal lighting conditions year-round. In an automated greenhouse, growers can keep their light fixtures on a timer, coordinating them with these various elements as they change.
Along with superior growth, this allows operations to keep their energy consumption to a minimum. Electricity costs can quickly get out of hand in larger-scale structures, but if growers are optimizing their light fixtures to run as needed, then they will use only what’s required to produce high-quality yields.
For growers that rely on light deprivation, an automated greenhouse can also be valuable for effortlessly maintaining stringent lighting schedules. While other operations are stuck manually pulling tarps at a set time each day, automated light dep systems can be programmed to open and close on their own. This is generally more effective for creating blackout conditions and can free up a significant amount of time.
TEMPERATURE CONTROL
Since different crops perform better in various climates, growers can use automation to dial in their greenhouse environment as needed, with little time or effort. This can be accomplished in several ways, whether growers are heating in winter or trying to optimize cooling efforts amidst higher temperatures.
During winter, growers can force their heating system to turn off once a set temperature point has been reached. With rising utility prices and a large-scale space to heat, this feature is more important than ever for commercial growers to conserve fuel and improve their bottom line.
The same reality also pertains to growers in hotter climates, as running a cooling system all day can require substantial amounts of electricity. In fact, rather than relying solely on wet walls or ventilation, growers should complement their space with an automated shade system.
Just like light deprivation kits, these can be deployed at pre-determined times to shield crops from the sun’s heat and help maintain interior temperatures. Having a high-quality shade system that’s programmed to operate on its own will require little labor, help reduce cooling costs and support healthy crop growth.
Regardless of where or what operations are growing, automation will give them the ability to control systems and create an ideal environment for their crops. With help from an environmental controller, they can ensure their automated greenhouse is monitored and controlled at all times, producing consistent harvests and reducing the overall cost to run their operation.
The content & opinions in this article are the author’s and do not necessarily represent the views of AgriTechTomorrow
Comments (0)
This post does not have any comments. Be the first to leave a comment below.
Featured Product
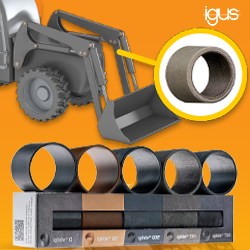